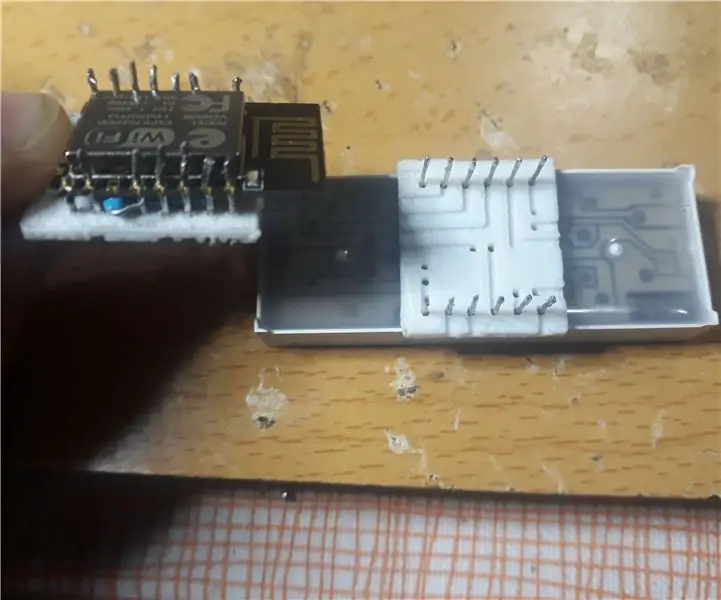
Cuprins:
2025 Autor: John Day | [email protected]. Modificat ultima dată: 2025-01-23 15:04
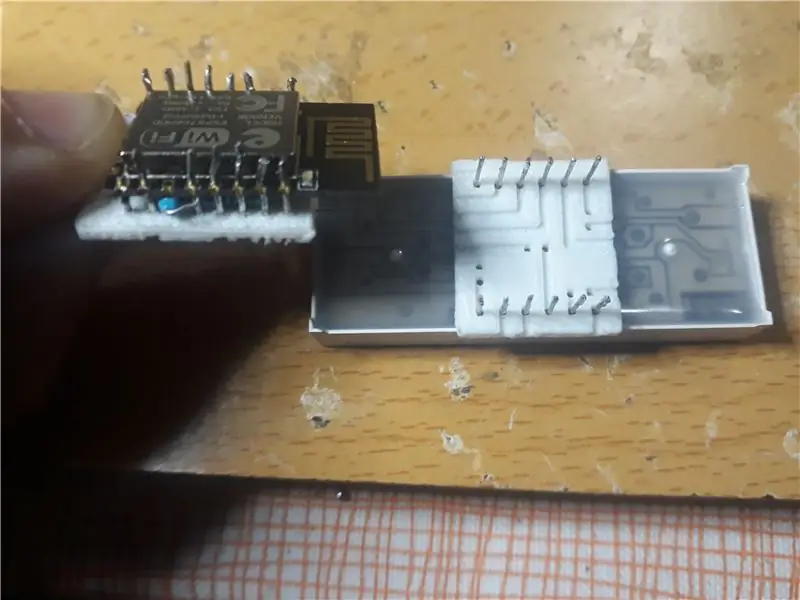
Când am ajuns să conectez un ecran cu 4 cifre și 7 segmente la Teensy, am decis că trebuie să încep cercetarea modului de fabricare a PCB-urilor acasă într-un fel ușor. Gravura tradițională este destul de plictisitoare și periculoasă, așa că am aruncat rapid asta. O idee bună pe care am văzut-o în jur sunt plăcile imprimate 3D care funcționează adăugând vopsea conductivă canalelor dvs., dar acest lucru pare destul de neregulat pentru conductivitate. Există, de asemenea, filamente conductive speciale pe care le-ați putea folosi pe o imprimantă cu extrudare dublă, dar caut ceva de bază și eficient pentru echipamentul standard pe care îl am.
Așa că m-am gândit să lipiți direct și să puneți componente și conectori pe imprimările 3D.
Înainte de a începe, fiți avertizați: vom imprima cu ABS deoarece poate face față + 200 ° C înainte de deformare (astfel încât să putem aplica cu atenție o lipire peste el). Imprimarea cu ABS nu este la fel de simplă ca și cu PLA, aveți nevoie de o imprimantă închisă și de multe calibrări de setări, dar odată ce ați reușit acest lucru, rezultatul face diferența.
Pentru a adăuga un anumit context, în exemple, creez un PCB pentru placa wifi ESP8266 12E, astfel încât să îl pot conecta cu ușurință la orice altceva mai târziu (scopul final este un afișaj 4d7seg).
PCB-ul îmi va permite să folosesc toți pinii disponibili, în timp ce majoritatea modulelor de acolo au foarte puțini pini de rezervă sau au prea multe caracteristici suplimentare pe care nu le doresc cu adevărat (cum ar fi NodeMCU).
Provizii
- Software de proiectare PCB (KiCad aici, gratuit). Nivelul de start.
- Software de modelare 3D (Blender aici, gratuit). Nivel utilizator.
- O imprimantă 3D (Creality 3D Ender 3 Pro aici, aproximativ 200 €). Nivel utilizator.
- O carcasă pentru imprimantă este foarte recomandată atunci când utilizați ABS - Asigurați-vă că puteți imprima cu succes ABS înainte de a continua acest instructable.
- Filament ABS (Smartfil ABS, aproximativ 20 € / Kg). 3-15 grame pe PCB.
- Ace de cusut (ia doar câteva de la mama). Dimensiunea va depinde de diametrul pinilor componentelor dvs. De obicei, diametrul de 0,5 mm sau 1 mm.
- Lamină de tablă și sudor (aproximativ 15 € de la un magazin local). În plus, toate accesoriile potrivite pentru sudare: suport pentru sudor, o lampă, o placă, o pensetă, ochelari de protecție, o mască … accesoriile depind de utilizator, asigurați-vă că vă simțiți confortabil și în siguranță în timpul lucrării!
- Multă răbdare, o minte creativă și o bază bună (încercați să faceți google și să studiați mult înainte de a pune mâna pe tine).
Pasul 1: Prototip și schemă
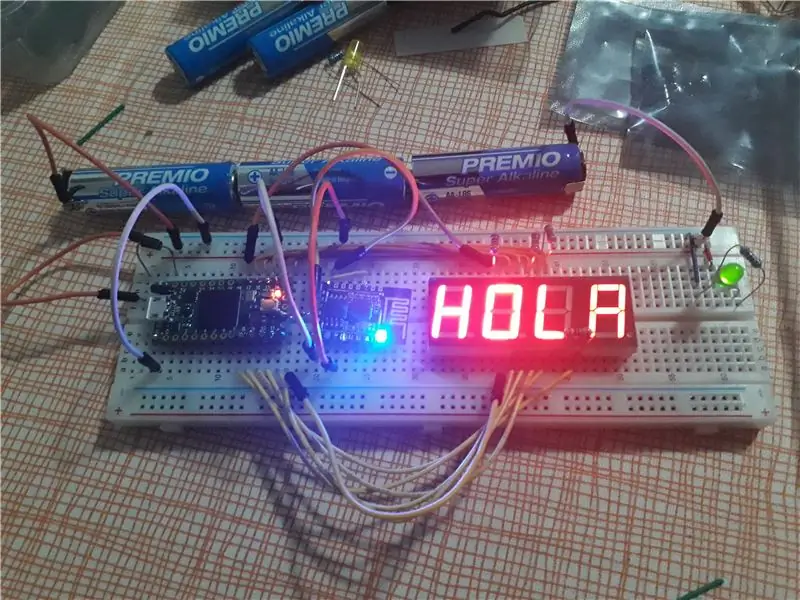
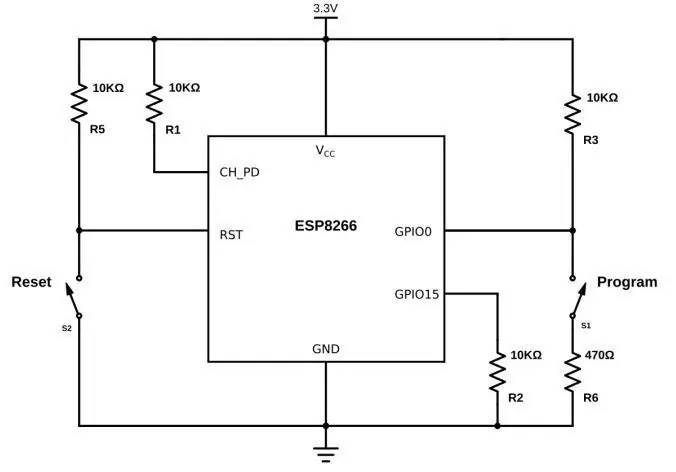
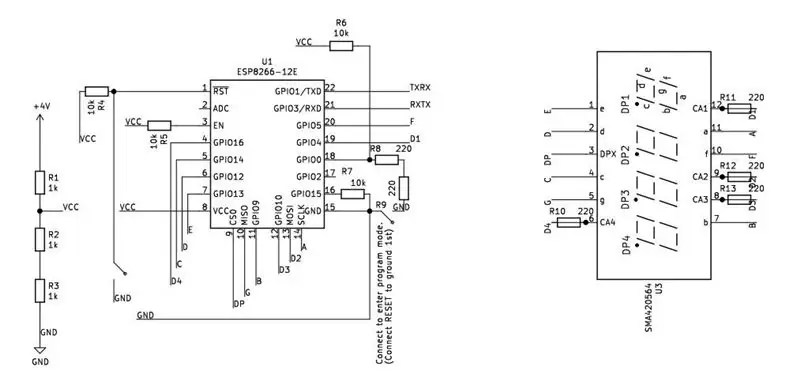
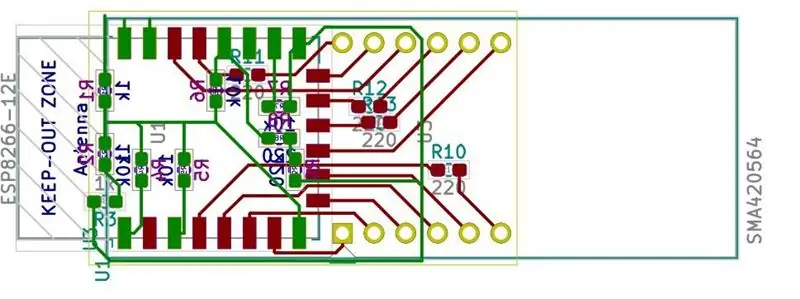
Dacă nu urmăriți schema altcuiva, ar trebui să vă construiți circuitul electric urmând specificațiile producătorului. Testați un circuit prototip și, după ce îl funcționați, schițați toate conexiunile și componentele.
Odată ce ai o schiță și te simți confortabil cu o înțelegere clară a circuitului tău, descrie-l în detaliu în software-ul tău preferat EDA. Acest lucru vă va ajuta să optimizați și să vă verificați designul.
Desenați schema și folosiți-o ca ghid pentru proiectarea PCB-ului. Software-ul EDA, cum ar fi Eagle sau KiCad, vă va permite să adăugați componentele dvs. specifice, cu pini și dimensiuni realiste, astfel încât să puteți proiecta circuitul dvs. electric în jurul lor.
Folosesc KiCad, care este gratuit și ușor de înțeles pentru un starter. Tot ce știu este mulțumit lui Brian Benchoff @ https://hackaday.com/2016/11/17/creating-a-pcb-in… și unor postări conexe, așa că urmați liniile directoare pentru a ajunge la un design frumos al PCB-ului.
Imaginile din această secțiune se referă la:
- Testați prototipul pentru ESP8266 și un afișaj cu 4 cifre din 7 segmente (atașat la un Teensy 4).
- O schemă de cablare de referință pentru o placă wifi ESP8266 12E.
- O schemă KiCad pentru un afișaj de 4 cifre cu 7 segmente care funcționează prin ESP8266 și un divizor de tensiune (acesta este scopul meu final).
- O ieșire de proiectare KiCad PCB.
Pasul 2: Model 3D
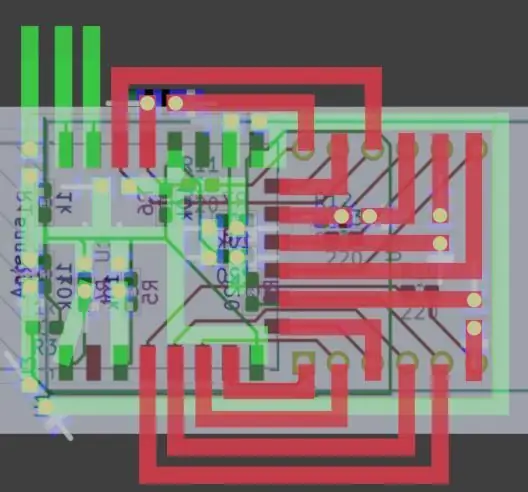

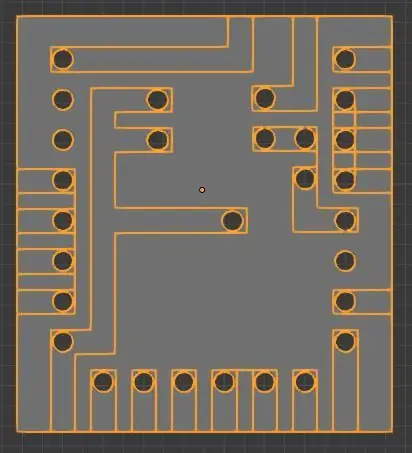
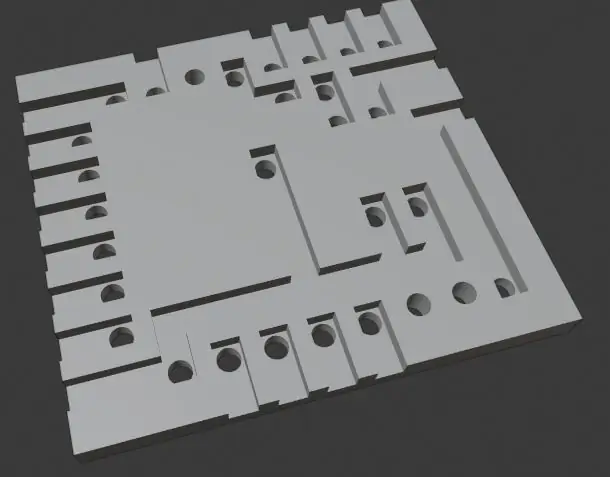
Odată ce aveți un design PCB pe hârtie, ar trebui să-i oferiți ceva mai mult realism într-un software de modelare 3D. Acest lucru vă va pregăti, de asemenea, fișierul pentru imprimanta 3D. Acesta este modul în care o fac în Blender:
- Creați o plasă plană și adăugați imaginea dvs. de design PCB peste ea. Asigurați-vă că este la scară și dimensiunile sunt realiste, deoarece aceasta va servi drept „hârtie de calc”.
-
Creați componente simplificate, acordând o atenție specială locației și dimensiunii exacte a codurilor PIN care se conectează la PCB. Obțineți specificațiile producătorului online sau măsurați-le singur pentru a le obține suficient de precise. Rețineți câteva dimuri standard pe care le puteți folosi ca referință:
- Pentru scânduri folosiți avioane. Pentru un PCB cu o singură față, folosesc 1,5 mm grosime, la fel de subțire decât aceasta, nu am obținut detalii bune la imprimare (depinde și de setările și capacitățile imprimantei, dar vom trece la asta mai târziu). Pentru un PCB cu două fețe am folosit grosimea de 2,5 mm.
- Pentru știfturi folosiți cilindri, cu diametrul de minimum 1 mm pentru a fi captat de imprimantă.
-
Pentru canale utilizați cuburi, cu lățimea de minimum 1,2 mm. Veți extruda doar fețele pentru a vă obține canalele.
- Localizați componentele în funcție de designul PCB-ului. Dacă componentele dvs. sunt suficient de realiste, puteți utiliza acest lucru pentru a verifica dacă există ciocniri, dar permiteți întotdeauna spațiu suplimentar în jurul fiecărui element.
- Urmăriți circuitul electric. Așezați o plasă cub în locul primului știft. Apoi, în modul de editare, extrudați fețele în linie dreaptă după proiectare. Din nou, păstrați-l simplu, folosind linii de 90 ° și utilizați câte canale considerați. De asemenea, permiteți o separare de cel puțin 0,8 mm între pereți sau în caz contrar aceștia vor pierde la imprimare. Imaginea 1 de mai jos prezintă câteva trasee modificate după modelare cu dimensiuni reale, deoarece traseul ideal era prea subțire pentru a fi posibil.
- Creați PCB adăugând un cub plat (dim ca mai sus).
- Gravează-ți canalele și găurile pe placă adăugând modificatori booleeni la obiectul tău PCB. Aceasta va tăia partea de bord care intersectează obiectul țintă al modificatorului boolean.
Imaginile 3 și 4 arată rezultatul final pentru placa ESP8266 (model 3D în imaginea 2).
După aceasta, ar trebui să vedeți o imprimare 3D a PCB-ului dvs.
Ultimul pas este exportul corect al modelului.
- Asigurați-vă că toate fețele sunt îndreptate spre exterior („Mod editare - Selectați toate” Apoi „Plasă - Normale - Recalculați în exterior”).
- Asigurați-vă că acestea sunt toate fețele individuale („Mod editare - Selectați toate” Apoi „Edge - Edge Split”).-- Dacă omiteți acești doi pași, este posibil să găsiți detalii lipsă pe software-ul dvs. Slicer.--
- Exportați ca. STL („Numai selecție” pentru a exporta doar PCB-ul final și „Scene Units” pentru a păstra scara lucrurilor).
Pasul 3: Slicer Software
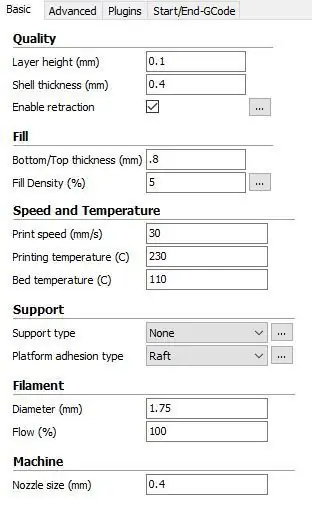
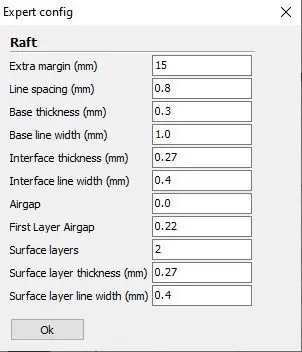
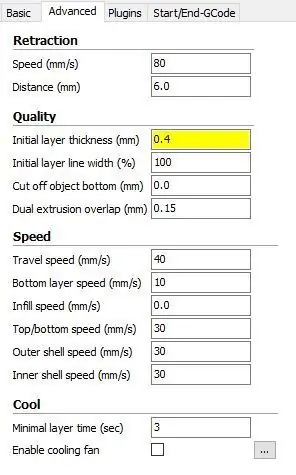
Imprimantele 3D oferă de obicei un software „Slicer” pentru a procesa modelele 3D (în format.stl sau alte formate) și pentru a calcula ruta necesară pentru imprimare (de obicei în format.gcode). Am un Creality Ender 3 și nu m-am mutat din Creality Slicer furnizat, dar puteți aplica aceste setări oricărui alt software.
Dedic o secțiune completă setărilor pentru feliere, deoarece acestea sunt foarte importante atunci când tipăriți ABS, ceea ce este destul de dificil din cauza deformării, micșorării și crăparii. Imprimarea unui PCB este, de asemenea, în limita imprimantelor 3D standard datorită preciziei necesare.
Mai jos vă împărtășesc setările pe care le folosesc pe Creality Slicer pentru imprimarea detaliată a PCB-urilor prin ABS. Acestea diferă de setările standard în:
- Pereți și straturi subțiri (pentru a oferi suficiente detalii - acest lucru ar putea necesita câteva iterații pentru rezultatul dorit, cu excepția cazului în care sunteți mulțumit de setările mele).
- Folosiți o plută. Cheia este pe bază, de care ar trebui să aveți grijă deosebită. (Permit un offset de 10 mm față de model pentru a evita orice deformare minimă care să afecteze imprimarea). De asemenea, nu există separări între liniile de plută pentru a obține o bază solidă bună. Dacă îți faci baza corect, totul este gata. Dacă vedeți colțuri care se pliază în baza dvs., sunteți condamnat.
- Viteza mica. Folosesc aproximativ 1/4 din viteza standard (acest lucru permite o bună așezare a filamentelor și, prin urmare, lipirea și calitatea generală).
- Temperaturile ABS (pat: 110ºC, duza: 230ºC)
- Ventilator dezactivat (recomandat pentru menținerea temperaturii constante pentru ABS).
Pasul 4: Imprimați
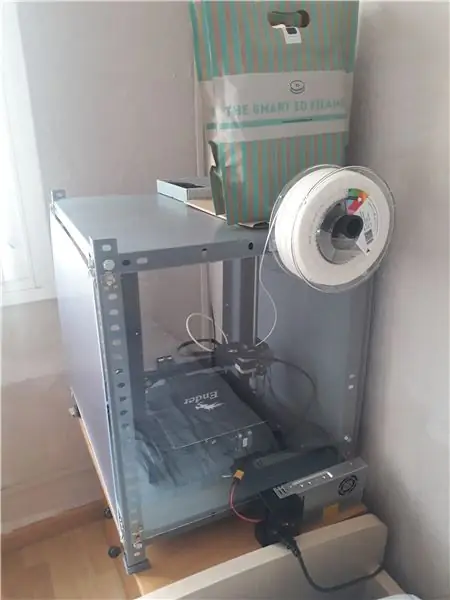
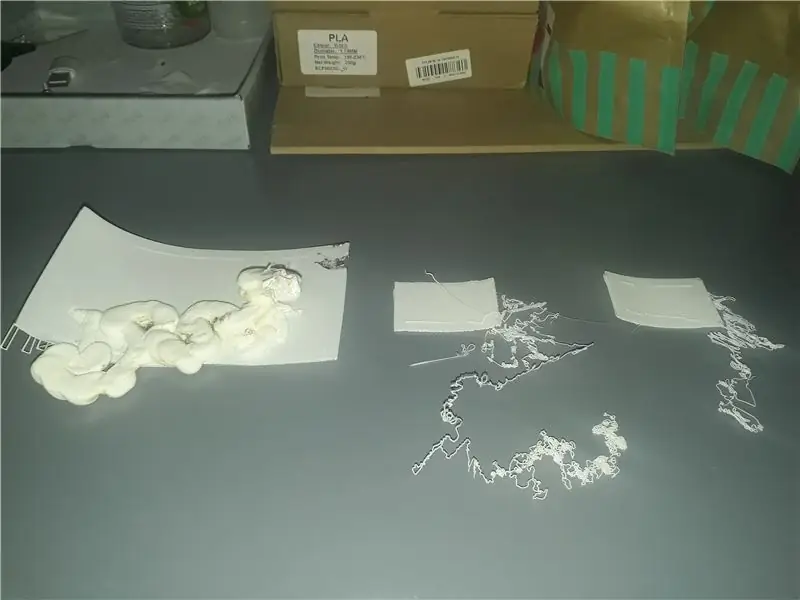
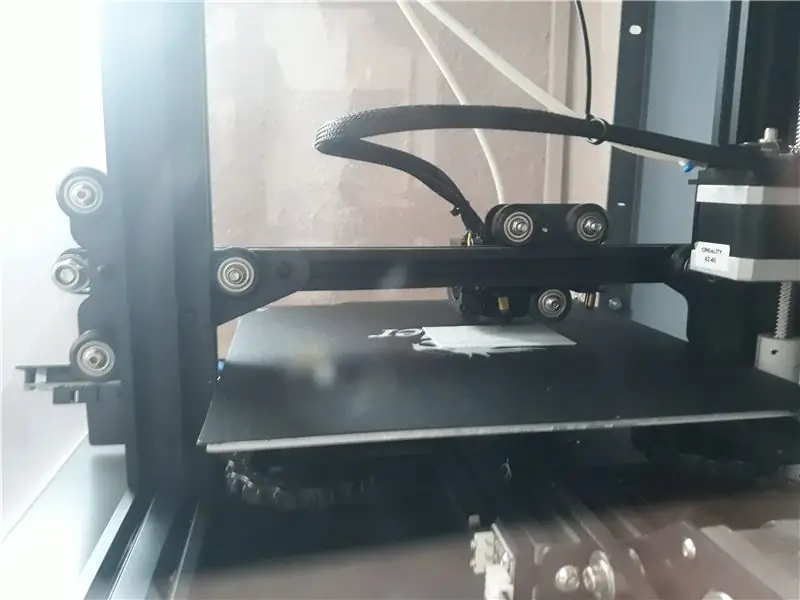
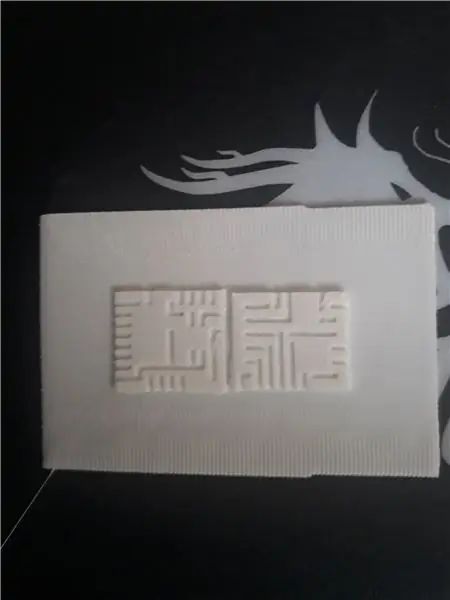
În cele din urmă, trimiteți-vă codul.g la imprimantă și fabricați PCB-ul. Câteva sfaturi pe care ar trebui să le urmați:
- Includeți imprimanta 3D. O carcasă vă va menține temperatura mult mai stabilă, ceea ce este o cerință puternică pentru imprimarea ABS. Asigurați-vă că păstrați CPU și sursa de alimentare în afara carcasei, precum și a filamentului. Dacă reușiți să imprimați ABS fără o carcasă, vă rog să vă împărtășiți trucul, deoarece mă înnebunește.
- Preîncălziți imprimanta pentru o vreme. Pe PLA puteți imprima imediat, dar cu ABS sfatul meu este să preîncălziți cu setările ABS (pat: 110 ° C, duza: 230 ° C) timp de 10-15 minute, astfel încât să creați atmosfera potrivită înainte de a putea merge mai departe și de a începe imprimarea.
- Imprimați încet, dar sigur. După cum sa menționat mai devreme, am redus viteza de imprimare standard la 1/4 în fișierul de configurare. Acest lucru se dovedește a fi suficient de lent pentru a avea un rezultat bun, dar puteți gestiona viteza de imprimare în timp ce tipăriți reglând viteza de avans, dacă doriți să o optimizați un pic mai mult. Rețineți că viteza ridicată va duce la mișcări foarte bruște, care nu vor depune filamentul în mod eficient sau ar putea să se ciocnească de plasă și să-l desprindă.
- Construiește o bază bună. Cheia ABS este să obțineți o bază bine fixată. Dacă baza eșuează și se desface, modelul a dispărut (vezi câteva încercări dezastruoase de mai jos). Cu sfaturile de mai sus (încastrare, preîncălzire și viteză lentă) ar trebui să obțineți o bază bună și un finisaj bun. Dar, spre deosebire de PLA, pe care îl las nesupravegheat ore în șir, ABS are nevoie de mai multă atenție.
- Fii vigilent, mai ales la început. Reiterând cele de mai sus, cheia este baza. Asigurați-vă că primul contur exterior este bine așezat. Acest lucru va conduce la restul aderenței primului strat. Uneori, filamentul nu se lipeste imediat sau este tras din locul său. Ar trebui să observați acest lucru suficient de curând pentru a corecta orice nivelare sau curățare a plăcii de bază. Aveți grijă întotdeauna la deformări, dacă vedeți colțurile în creștere, acestea vor sfârși probabil să dezlipească întreaga bază și să strice întreaga imprimare. Chiar dacă baza se menține în poziție, deformarea va face acest colț deformat.
Pasul 5: Sârmă și lipire
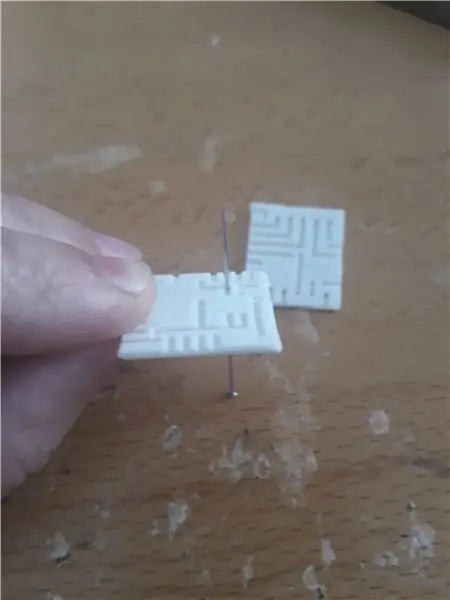
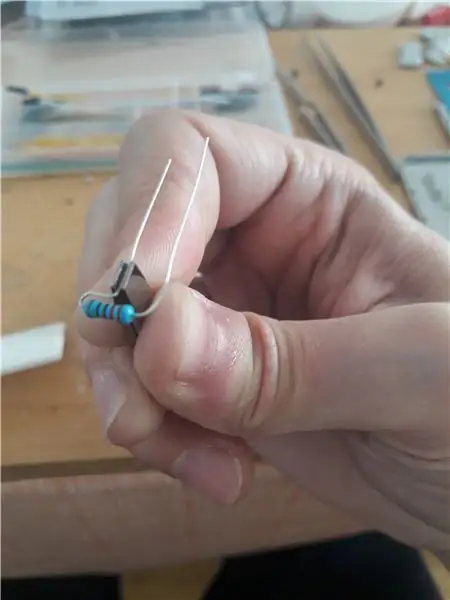
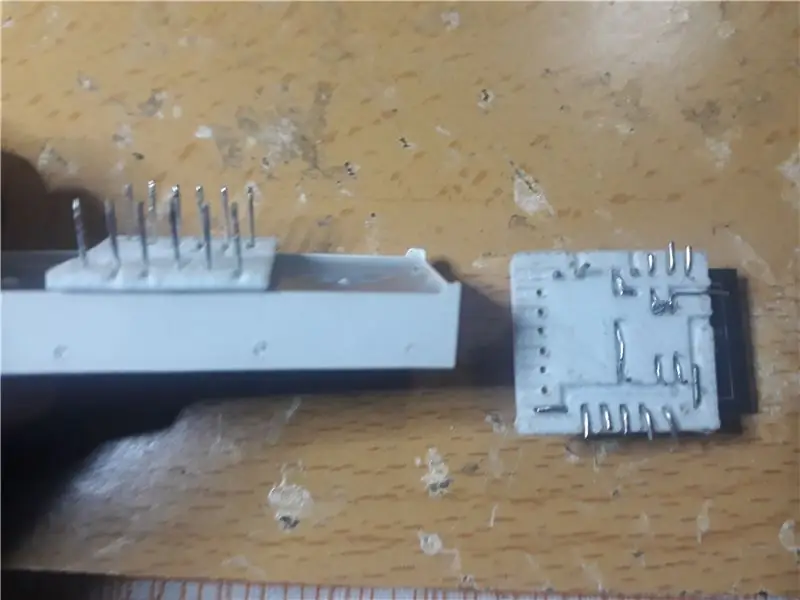
Acum este timpul să punem totul la punct:
- Verificați finisajul canalelor și găurilor. În mod special, găurile sunt omise sau suprapuse de imprimantă. Folosiți un ac de cusut dacă trebuie să redeschideți unele dintre acestea. Desigur, dacă nu ați obținut o imprimare plată din cauza deformării sau nu ați obținut detaliile pe care le așteptați, verificați din nou setările imprimantei sau chiar modelul 3D pentru dimensiuni.
- Așezați componentele. Modulele, rezistențele, condensatoarele sau ledurile care au propriile pini pot fi montate cu ușurință. Puteți îndoi ușor propriul fir pentru a-l introduce în canale, astfel încât să fie mai ușor să le legați mai târziu.
- Adăugați sârmă și lipiți. Utilizați orice știfturi sau jumperi care se încadrează în canal și tăiați-le lung, astfel încât trebuie doar să lipiți la punctele de joncțiune specifice. Nu ar trebui să lipim totul, deși tind să o fac când lucrurile nu se aprind.. În cazul meu, a trebuit să conectez toți pinii ESP8266, iar aici a fost esențial să abilități bune de lipit (ceea ce eu nu fac). Restul consiliului a fost destul de simplu de făcut.
Pasul 6: testați-vă tabloul
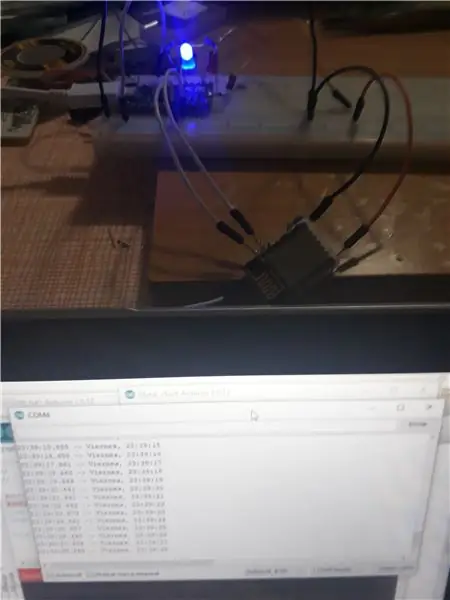
Dacă aveți încredere că ați făcut totul bine, conectați-l.
Pentru prototipuri rulez ESP8266 pe conexiunea serială Teensy 4.
În timp ce făceam testele pe placa goală, am încărcat un program care încărca ora locală prin wifi. După cum puteți vedea, totul a funcționat bine. Sper că ați avut un rezultat bun și cu această tehnică.
Recomandat:
Spirometru imprimat 3D: 6 pași (cu imagini)
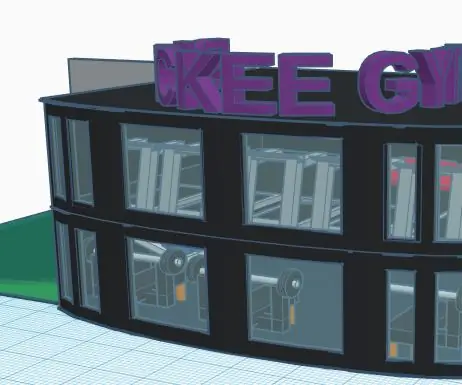
Spirometru tipărit 3D: Spirometrele sunt instrumentul clasic pentru a efectua analiza aerului pe măsură ce este suflat din gură. Acestea constau dintr-un tub în care suflați, care înregistrează volumul și viteza unei respirații, care sunt apoi comparate cu un set de valori normale de bază
Un instrument muzical electric Amplificator imprimat 3D: 11 pași (cu imagini)
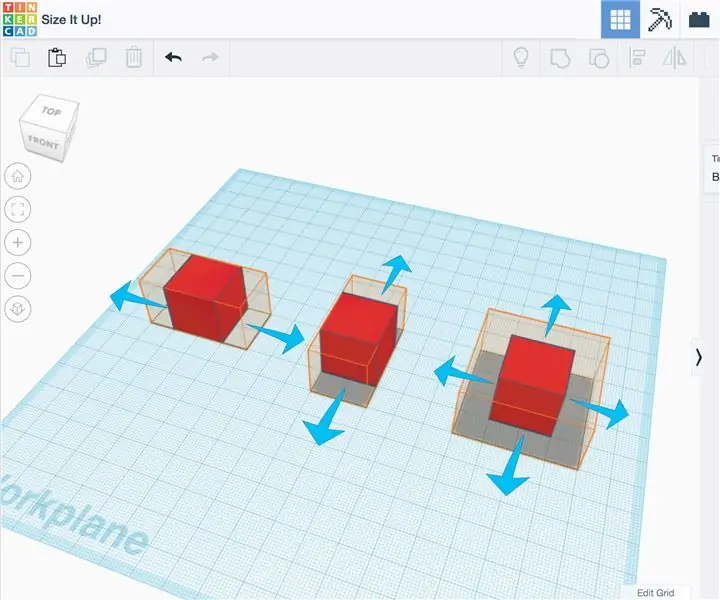
Un amplificator imprimat cu instrument muzical electric 3D: definirea proiectului. Sper să fac un amplificator imprimabil pentru a fi utilizat cu o vioară electrică sau orice alt instrument electric. Specificație. amplificator activ și mențineți-l mic.Ele
Power Bank sub 10 USD! - DIY - Imprimat 3D: 6 pași (cu imagini)
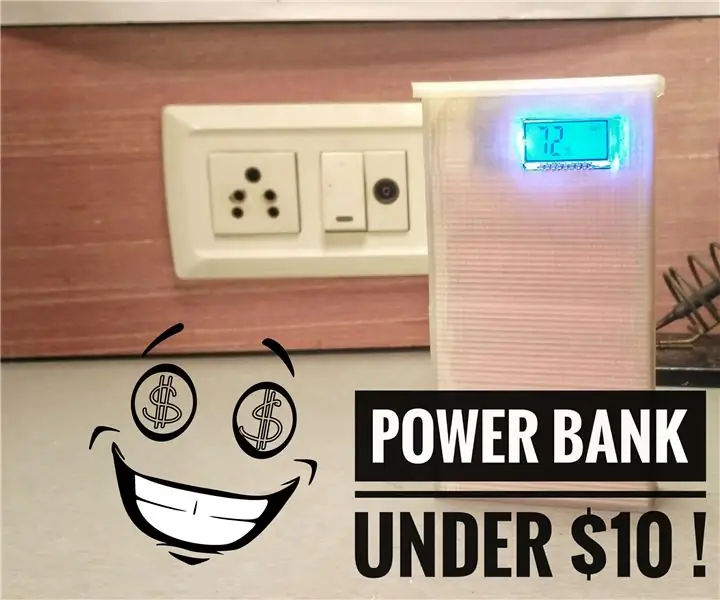
Power Bank sub 10 USD! | DIY | Imprimat 3D: industria smartphone-urilor de astăzi produce telefoane mult prea puternice decât ne așteptam în anii 90, dar nu există decât un singur lucru care le lipsește, adică bateria, acestea sunt cele mai grave. Și singura soluție pe care o avem acum este o bancă de putere. În acest videoclip, vă voi arăta cum
Robot cvadruped cu alimentare Arduino imprimat 3D: 13 pași (cu imagini)
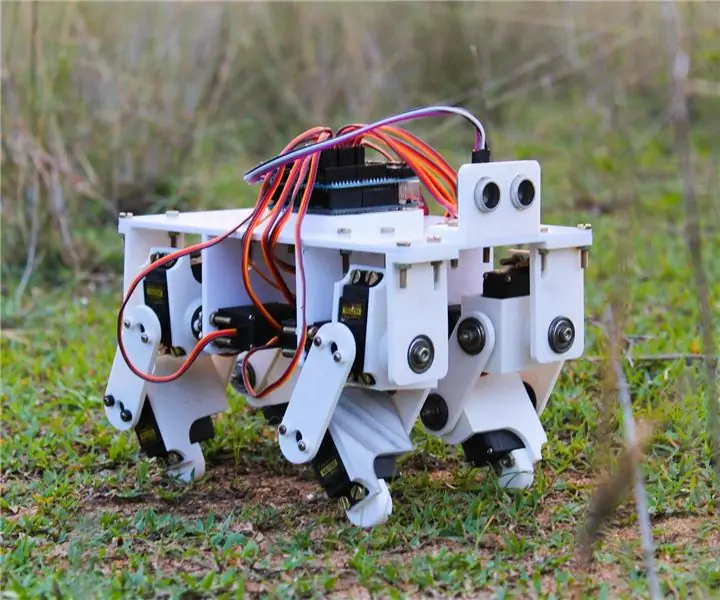
Robot cvadruped motorizat Arduino imprimat 3D: din instructabilele anterioare, puteți vedea probabil că am un profund interes pentru proiectele robotice. După instruirea anterioară, unde am construit un robot biped, am decis să încerc să fac un robot patruped care să poată imita animale precum câinele
Brat robotizat imprimat 3D Moslty care simulează controlerul de marionetă: 11 pași (cu imagini)
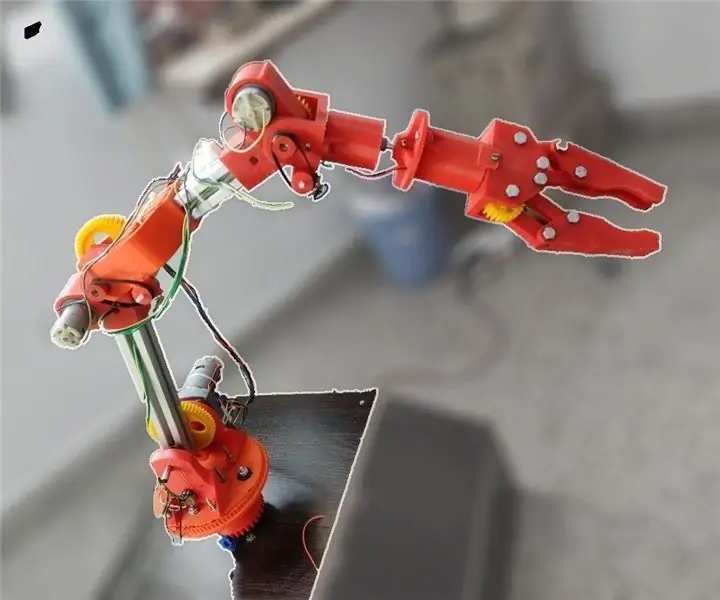
Moslty 3D Robotic Arm That Mimics Puppet Controller: Sunt un student de inginerie mecanică din India și acesta este proiectul meu de studii universitare. gripper. Brațul robotizat este controlat cu