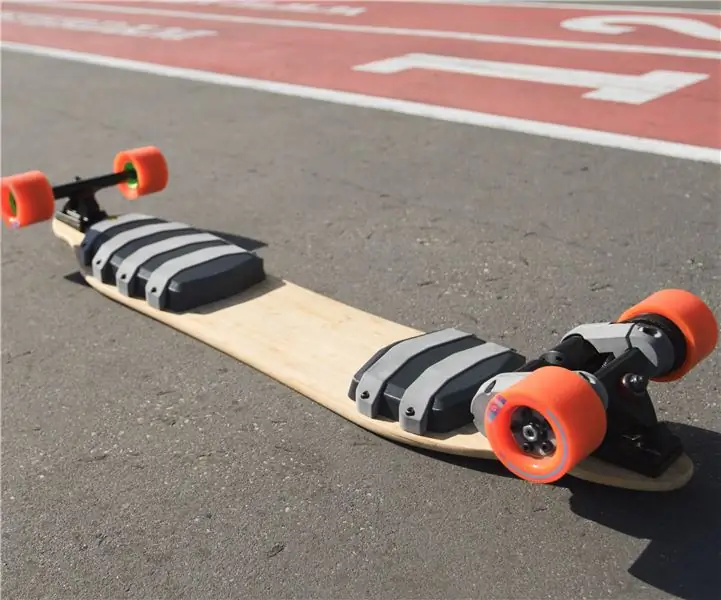
Cuprins:
2025 Autor: John Day | [email protected]. Modificat ultima dată: 2025-01-23 15:04
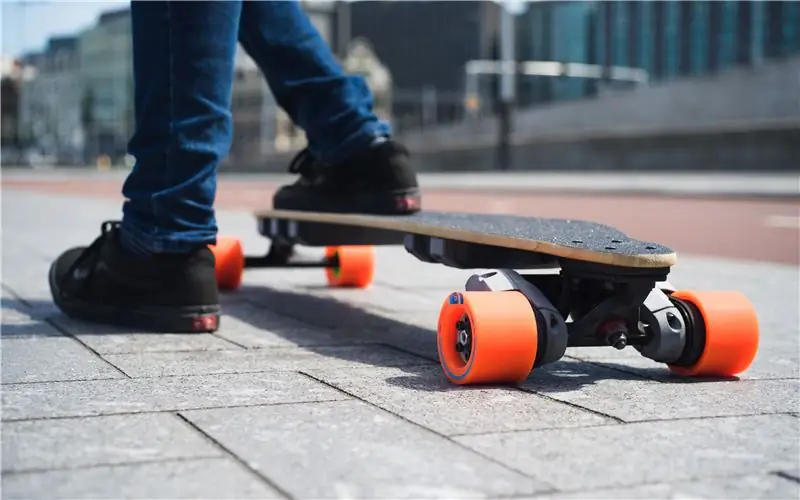
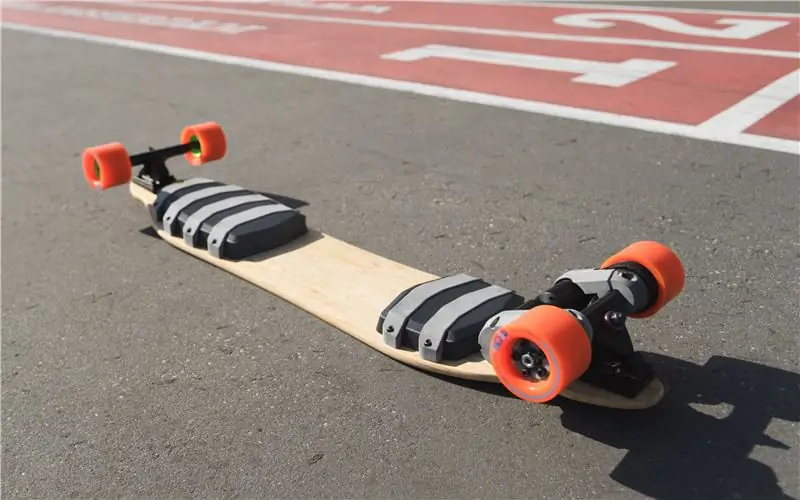
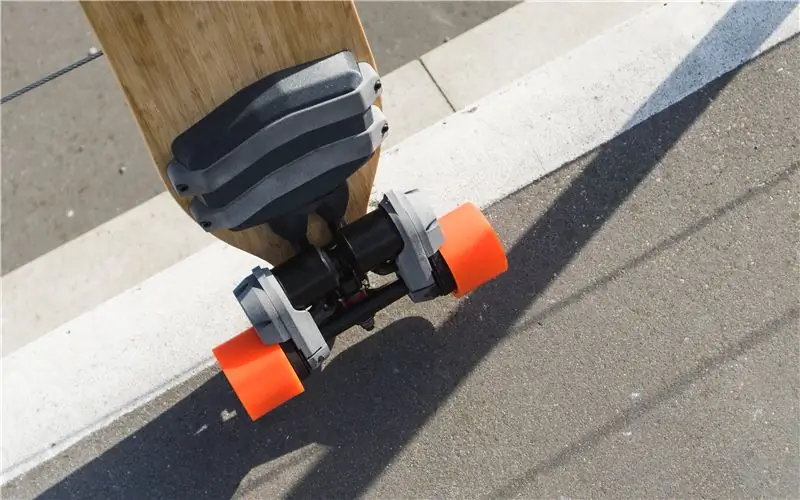
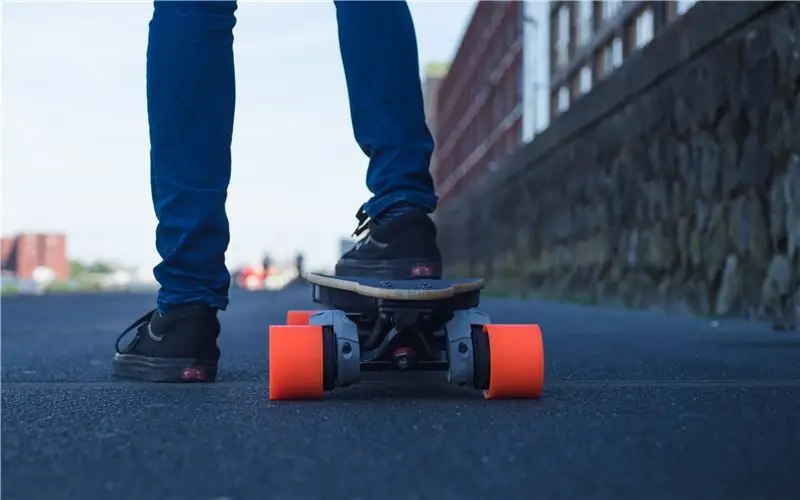
Acest Instructable este o prezentare generală a procesului de construcție pentru Fusion E-Board pe care l-am proiectat și construit în timp ce lucram la Hub-uri 3D. Proiectul a fost însărcinat să promoveze noua tehnologie HP Multi-Jet Fusion oferită de hub-urile 3D și să prezinte mai multe tehnologii de imprimare 3D și cum pot fi combinate eficient.
Am proiectat și construit un longboard electric motorizat, care poate fi folosit pentru călătorii scurte până la moderate sau combinat cu transportul public pentru a oferi o gamă de călătorii mult mai largă. Are o viteză maximă ridicată, este foarte manevrabil și este ușor de transportat când nu este utilizat.
Pasul 1: Procesul de proiectare
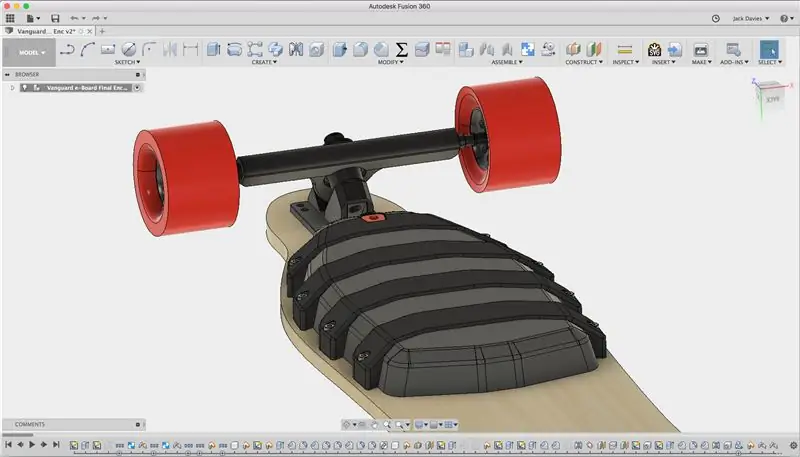
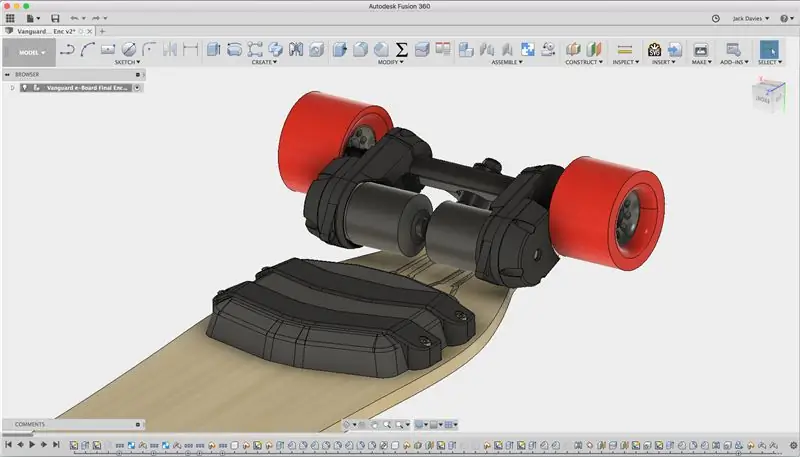
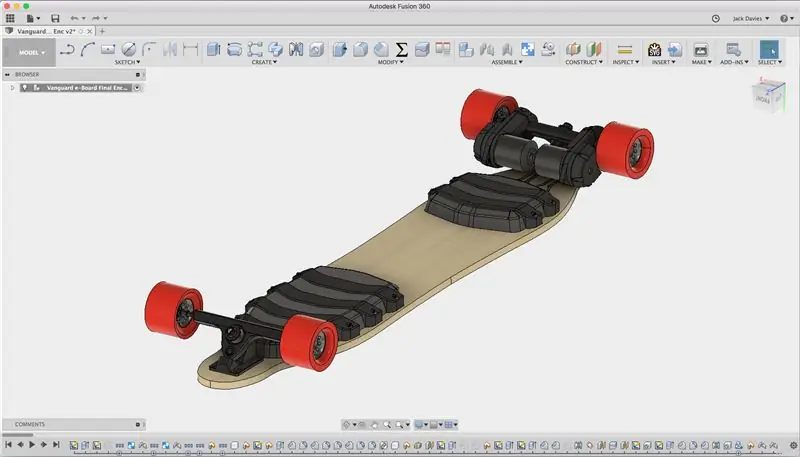
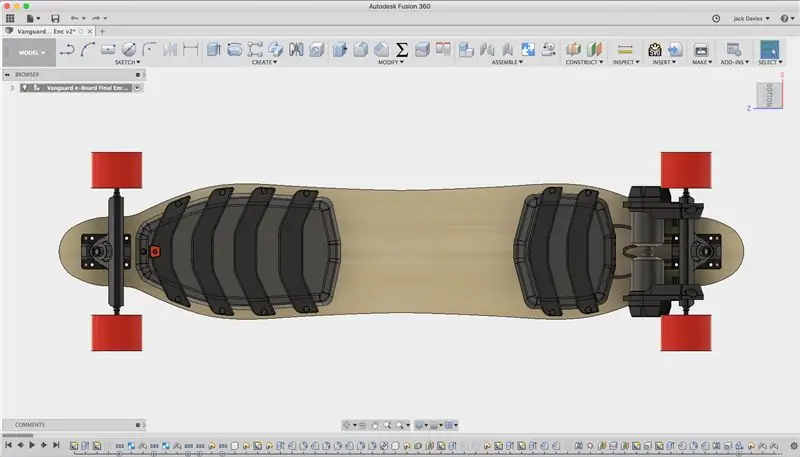
Am început proiectul identificând principalele componente standard ale longboard-ului; camioane, punte și roți. Acestea erau de pe raft, așa că le-am folosit ca punct de plecare al proiectării. Prima etapă a fost proiectarea transmisiei, care include suporturile motorului, configurarea angrenajului și a inclus unele modificări la camioane. Dimensiunea și poziția suporturilor motorului ar dicta dimensiunea și locația carcaselor, deci era important ca aceasta să fie finalizată mai întâi. Am calculat cerințele dorite de viteză maximă și cuplu, ceea ce mi-a permis apoi să selectez motoarele și bateria pentru placă. Raportul de angrenare a fost, de asemenea, calculat și au fost selectate dimensiunile fuliei, împreună cu lungimea curelei de transmisie. Acest lucru mi-a permis să calculez dimensiunea corectă a suporturilor motorului, care au asigurat o curea bine tensionată.
Următoarea etapă a fost proiectarea carcasei bateriei și a regulatorului de viteză (ESC). Puntea selectată este formată în principal din bambus, deci este destul de flexibilă, îndoindu-se substanțial în mijloc. Acest lucru are avantajele de a fi confortabil de condus, deoarece absoarbe umflăturile de pe drum și nu le transferă călărețului. Cu toate acestea, acest lucru înseamnă, de asemenea, că este necesară o carcasă divizată pentru a găzdui bateria și dispozitivele electronice, deoarece o carcasă pe toată lungimea nu ar putea să se flexeze cu placa și ar intra în contact cu solul în timpul funcționării. Controlerele electronice de viteză (ESC) au fost plasate cel mai aproape de motoare din cauza constrângerilor electrice. Deoarece motoarele sunt atașate prin intermediul camioanelor, poziția se schimbă în timpul virajelor, astfel că carcasa a trebuit să fie proiectată pentru a permite spațiul liber al motoarelor.
Sistemul de baterii a fost plasat la celălalt capăt al punții și a adăpostit componentele electronice legate de putere. Aceasta a inclus pachetul de baterii, format din 20 de celule 18650 litiu-ion, sistemul de gestionare a bateriei, comutatorul de pornire / oprire și priza de încărcare.
Am folosit Autodesk Fusion360 pentru întregul proces de proiectare, acest software mi-a permis să modelez rapid componente în interiorul ansamblului principal, ceea ce a accelerat considerabil timpul de dezvoltare. De asemenea, am folosit funcțiile de simulare din Fusion360 pentru a mă asigura că piesele vor fi suficient de puternice, în special suporturile motorului. Acest lucru mi-a permis să reduc de fapt dimensiunea monturilor, deoarece am putut verifica cerințele de rezistență și deviere și a elimina materialul, menținând în același timp un factor de siguranță adecvat. După finalizarea procesului de proiectare, a fost foarte ușor să exportați piesele individuale pentru imprimarea 3D.
Pasul 2: Transmisie
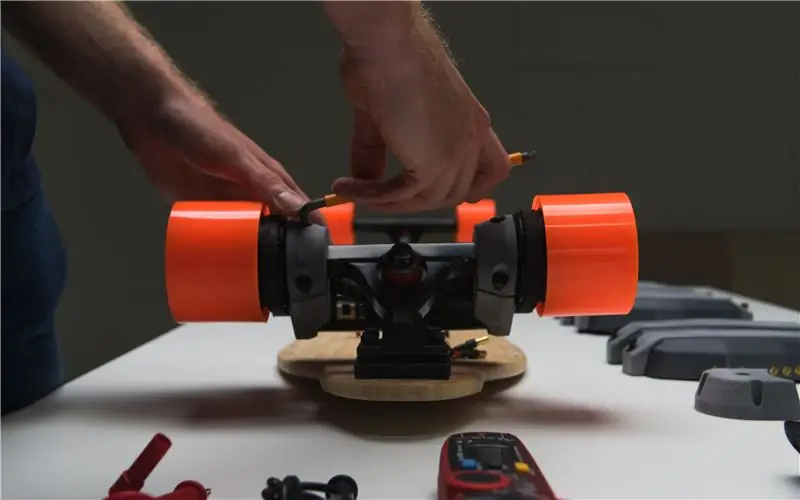
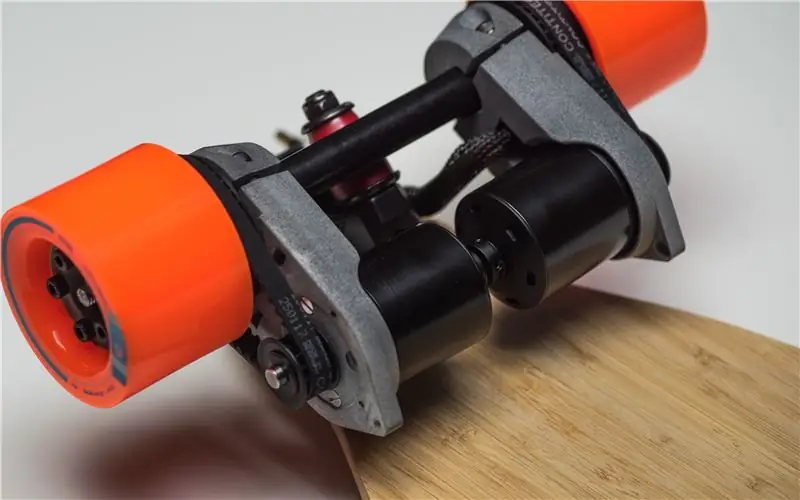
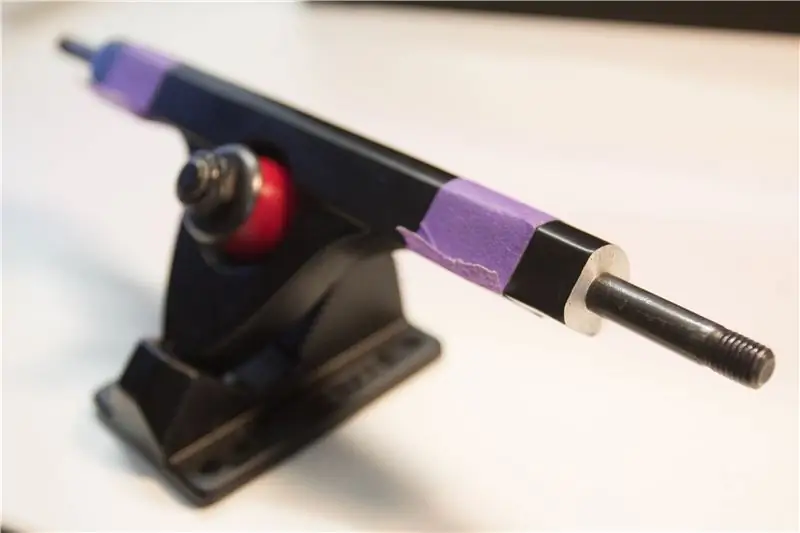
Am finalizat mai întâi construcția transmisiei, pentru a asigura o distanță adecvată pentru carcasa electronică. Am selectat camioane Caliber pentru a le folosi, deoarece au un profil pătrat care era perfect pentru prinderea suporturilor motorului. Cu toate acestea, axa a fost puțin prea scurtă pentru a permite utilizarea celor două motoare pe același camion, așa că a trebuit să extind acest lucru pentru a permite roților să se potrivească.
Am realizat acest lucru tăind o parte din corpul cuierului din aluminiu, expunând mai mult din puntea de oțel. Am tăiat apoi cea mai mare parte a axului, lăsând în jur de 10 mm pe care să-i pot fileta apoi cu o matriță M8.
Un cuplaj ar putea fi apoi înșurubat și o altă axă filetată adăugată la aceasta, extinzând efectiv axul. Am folosit compusul de fixare Loctite 648 pentru a fixa permanent cuplajul și axa nouă pentru a mă asigura că nu se deșurubează în timpul utilizării. Acest lucru a permis celor două motoare să se potrivească pe camion și a oferit un spațiu liber pentru roți.
Transmisia a fost tipărită în principal utilizând tehnologia HP Multi-Jet Fusion, pentru a asigura rigiditatea și rezistența în timpul accelerării și frânării mari, unde vor fi transferate cele mai mari forțe.
O roată specială a fost proiectată pentru a se bloca în roțile din spate, care a fost apoi conectată la fulia motorului cu o curea HTD 5M. O copertă imprimată 3D a fost adăugată pentru a oferi protecție ansamblului fuliei.
Pasul 3: Carcase cu coaste
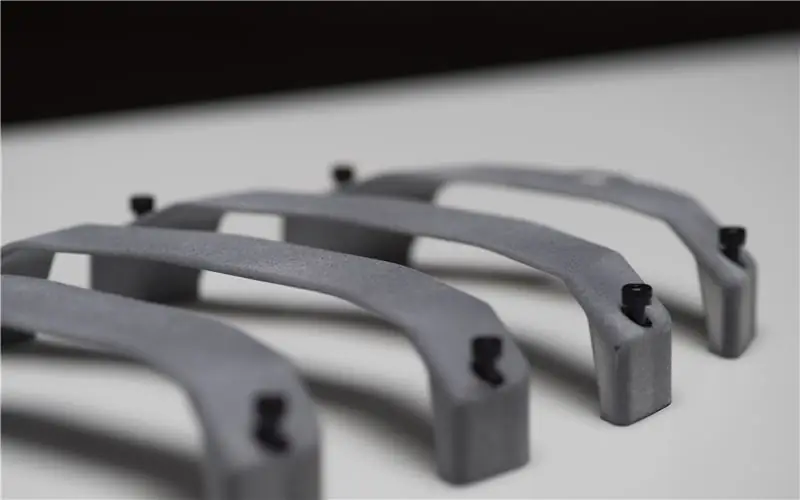
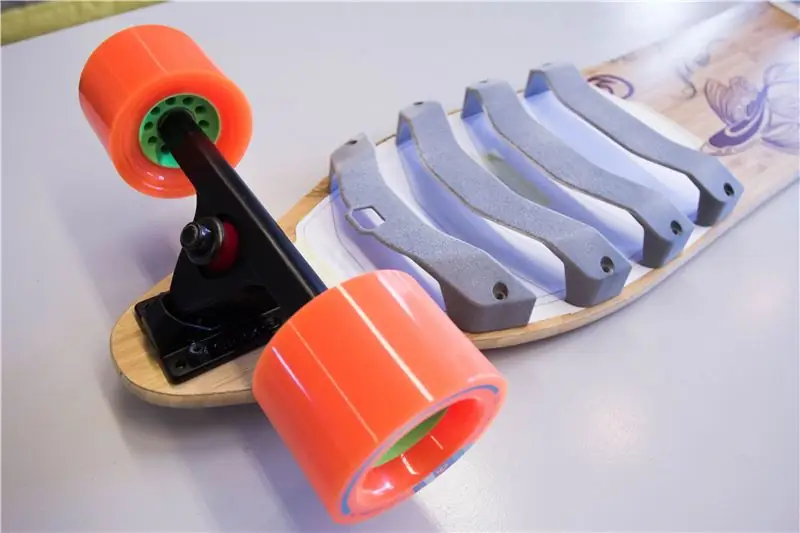
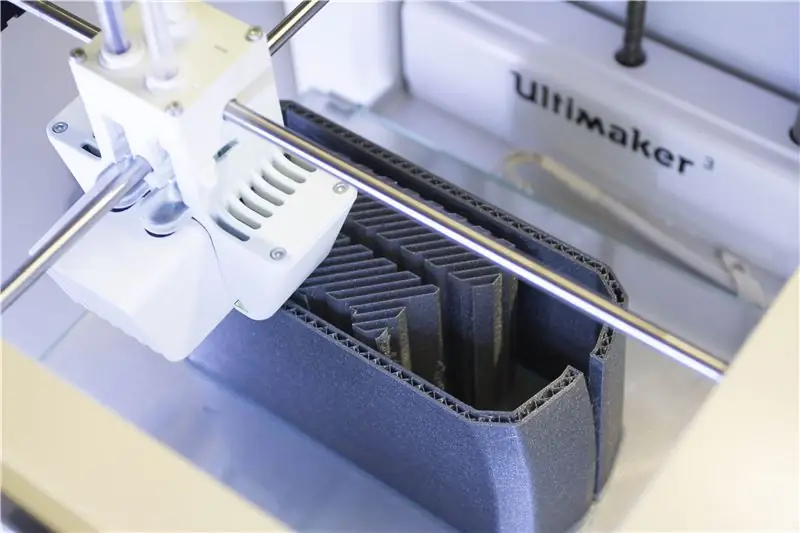
Una dintre principalele decizii de proiectare pe care am luat-o a fost separarea carcaselor, ceea ce a dus la un aspect curat și a permis punții flexibile să funcționeze fără nici o rigiditate suplimentară din carcase. Am vrut să transmit aspectele funcționale ale tehnologiei HP Multi Jet Fusion, așa că am decis să imprim FDM corpul principal al carcaselor, ceea ce a redus costurile, apoi am folosit piesele HP pentru a le sprijini și a le fixa pe punte. Acest lucru a oferit o estetică interesantă, fiind în același timp foarte funcțional.
Carcasele tipărite FDM au fost împărțite în jumătate pentru a ajuta la imprimare, deoarece materialul suport ar putea fi eliminat de pe suprafața exterioară. Linia de despărțire a fost poziționată cu atenție pentru a se asigura că a fost ascunsă de partea HP atunci când a fost prinsă pe placă. Au fost adăugate găuri pentru conexiunile motorului, iar conectorii glonți placați cu aur au fost lipiți pe loc
Inserții filetate au fost încorporate în puntea de bambus pentru a fixa carcasele de scândură și au fost șlefuite la nivelul suprafeței scândurii pentru a se asigura că nu există niciun spațiu între punte și incintă.
Pasul 4: Electronică
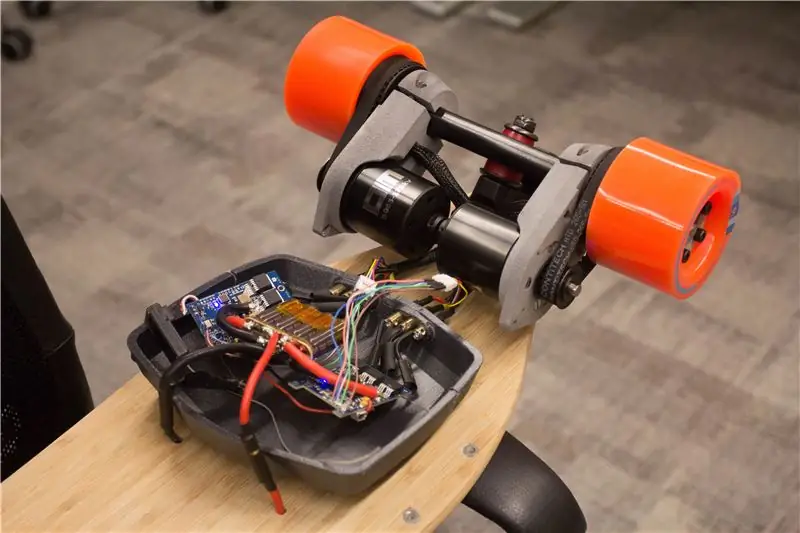
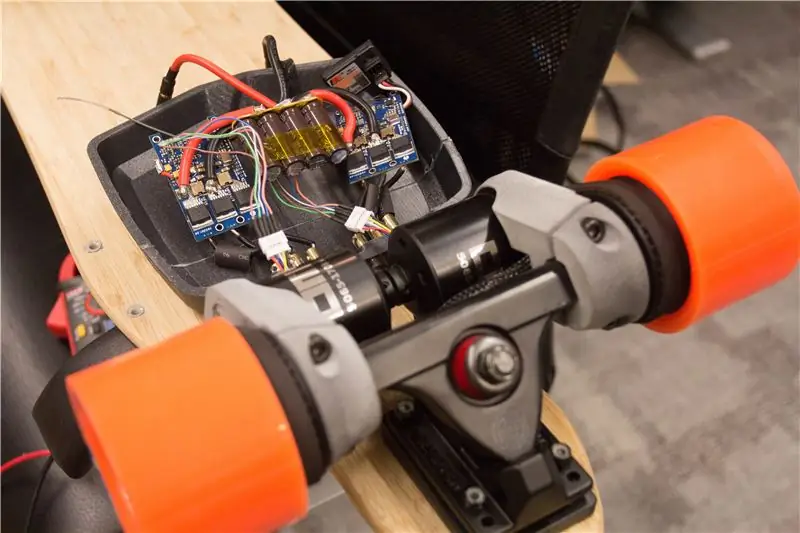
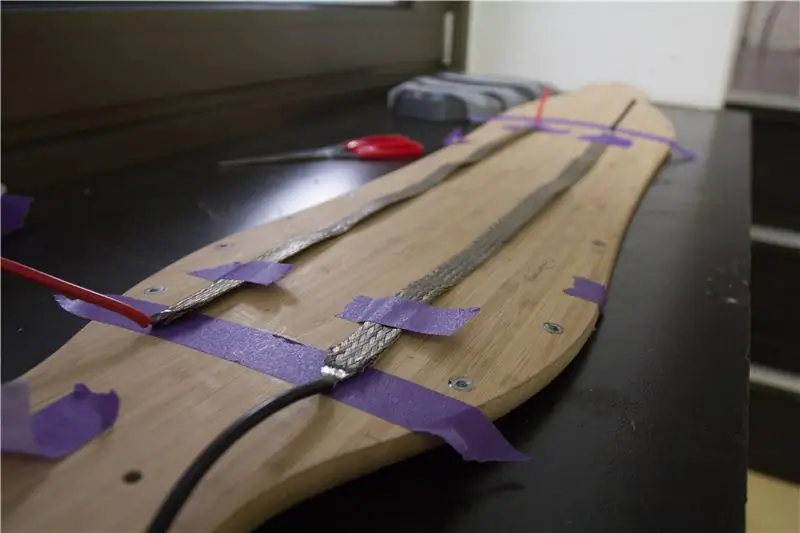
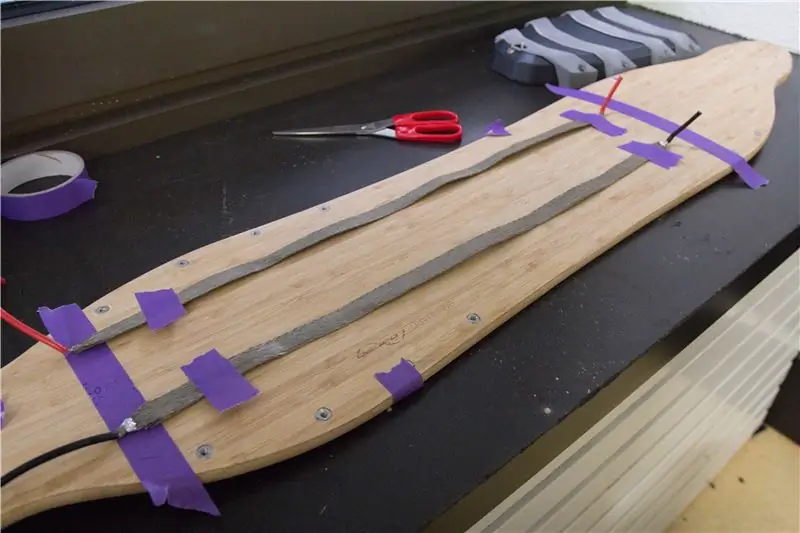
Electronica a fost aleasă cu atenție pentru a se asigura că placa este puternică, dar și intuitivă de utilizat. Această placă ar putea fi periculoasă dacă ar apărea defecțiuni, deci fiabilitatea este un factor foarte important.
Acumulatorul este alcătuit din 20 de celule litiu-ion 18650 individuale, care sunt sudate la punct pentru a forma un pachet de 42v. 2 celule sunt sudate în paralel și 10 în serie; celulele pe care le-am folosit au fost Sony VTC6. Am folosit un sudor cu puncte pentru a sudura filele de nichel pentru a forma pachetul, deoarece lipirea creează prea multă căldură care poate deteriora celula.
Puterea de la carcasa bateriei a fost transferată în cutia regulatorului de viteză folosind un cablu plan împletit care a fost trecut chiar sub banda de prindere din partea superioară a punții. Acest lucru a permis cablurilor să fie „ascunse” și a eliminat necesitatea de a rula cabluri pe partea inferioară, care ar fi arătat urât.
Deoarece aceasta este o placă cu motor dublu, sunt necesare două regulatoare de viteză pentru a controla independent fiecare motor. Am folosit regulatorul de viteză VESC pentru această construcție, care este un controller special conceput pentru skateboard-uri electrice, ceea ce îl face foarte fiabil pentru această utilizare.
Motoarele utilizate sunt 170kv 5065 out-runners, care pot produce 2200W fiecare, ceea ce reprezintă o mulțime de putere pentru această placă. Cu configurarea curentă a angrenajului, viteza maximă a plăcilor este de aproximativ 35MPH și accelerează foarte repede.
Ultima etapă a fost crearea unei telecomenzi pentru a controla placa. Un sistem wireless a fost preferat datorită funcționării mai ușoare. Cu toate acestea, a fost important să se asigure o fiabilitate ridicată a transmisiei, deoarece o scădere a comunicării ar putea avea probleme grave de siguranță, în special la viteze mari. După ce am testat câteva protocoale de transmisie radio, am decis că frecvența radio de 2,4 GHz va fi cea mai fiabilă pentru acest proiect. Am folosit un transmițător RC de pe raft, dar am redus semnificativ dimensiunea prin transferul electronicelor într-o carcasă mică de mână, care a fost imprimată 3D.
Pasul 5: Placă finalizată și videoclip promoțional
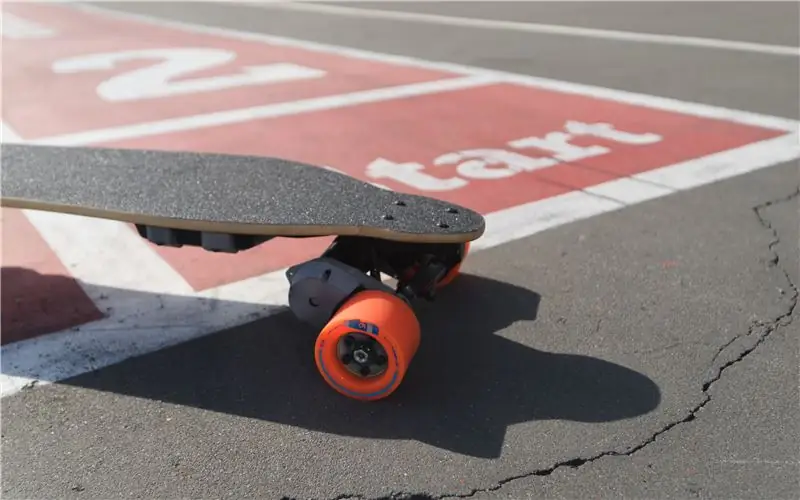
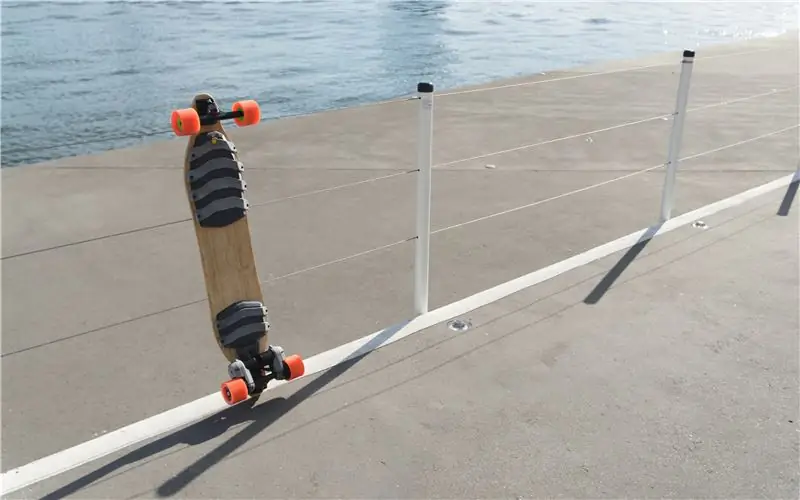
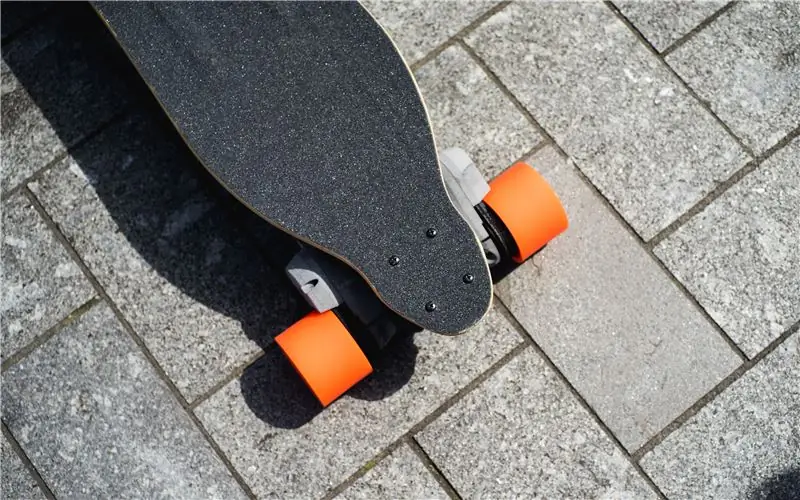
Proiectul este terminat! Am creat un videoclip destul de minunat al tabloului în acțiune, îl puteți vedea mai jos. Mulțumiri mari Huburilor 3D pentru că mi-ați permis să fac acest proiect - verificați-le aici pentru toate nevoile dvs. de imprimare 3D! 3dhubs.com
Recomandat:
Spirometru imprimat 3D: 6 pași (cu imagini)
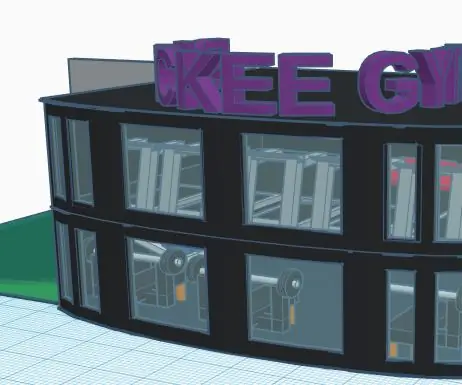
Spirometru tipărit 3D: Spirometrele sunt instrumentul clasic pentru a efectua analiza aerului pe măsură ce este suflat din gură. Acestea constau dintr-un tub în care suflați, care înregistrează volumul și viteza unei respirații, care sunt apoi comparate cu un set de valori normale de bază
Un instrument muzical electric Amplificator imprimat 3D: 11 pași (cu imagini)
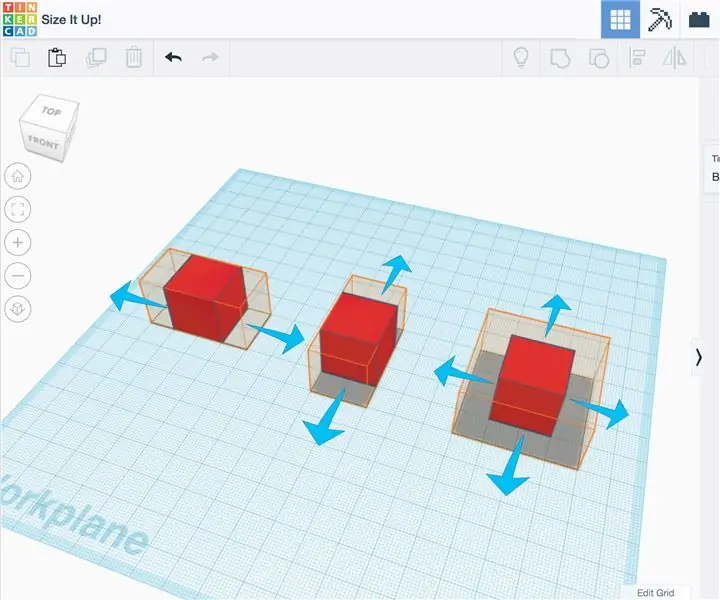
Un amplificator imprimat cu instrument muzical electric 3D: definirea proiectului. Sper să fac un amplificator imprimabil pentru a fi utilizat cu o vioară electrică sau orice alt instrument electric. Specificație. amplificator activ și mențineți-l mic.Ele
Power Bank sub 10 USD! - DIY - Imprimat 3D: 6 pași (cu imagini)
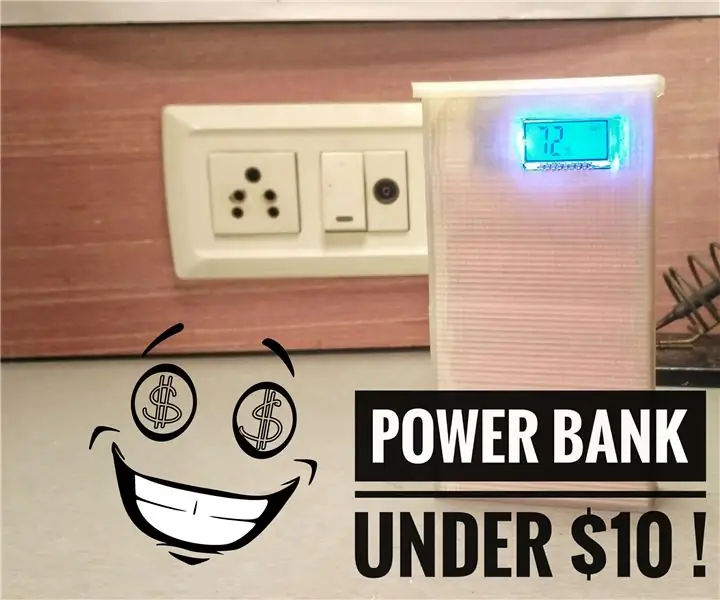
Power Bank sub 10 USD! | DIY | Imprimat 3D: industria smartphone-urilor de astăzi produce telefoane mult prea puternice decât ne așteptam în anii 90, dar nu există decât un singur lucru care le lipsește, adică bateria, acestea sunt cele mai grave. Și singura soluție pe care o avem acum este o bancă de putere. În acest videoclip, vă voi arăta cum
Robot cvadruped cu alimentare Arduino imprimat 3D: 13 pași (cu imagini)
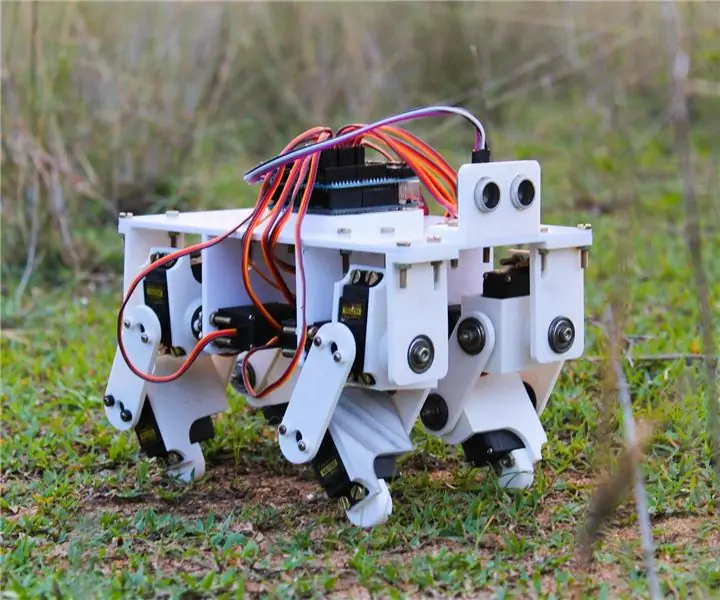
Robot cvadruped motorizat Arduino imprimat 3D: din instructabilele anterioare, puteți vedea probabil că am un profund interes pentru proiectele robotice. După instruirea anterioară, unde am construit un robot biped, am decis să încerc să fac un robot patruped care să poată imita animale precum câinele
Brat robotizat imprimat 3D Moslty care simulează controlerul de marionetă: 11 pași (cu imagini)
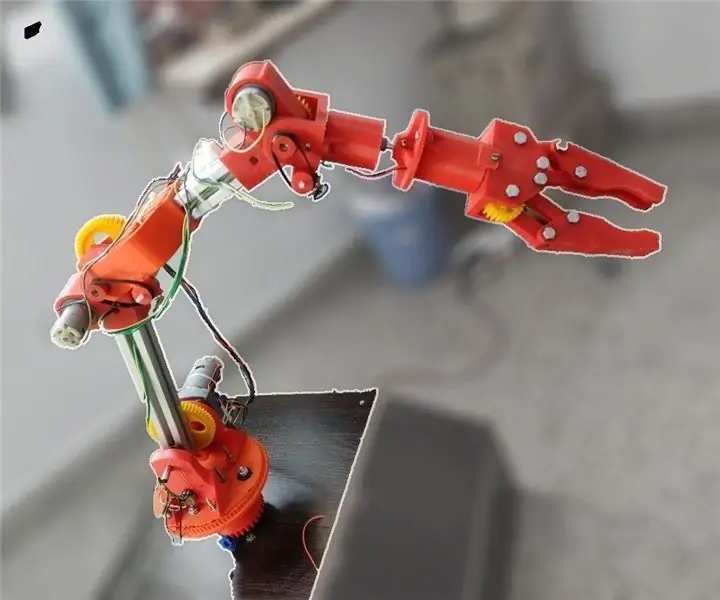
Moslty 3D Robotic Arm That Mimics Puppet Controller: Sunt un student de inginerie mecanică din India și acesta este proiectul meu de studii universitare. gripper. Brațul robotizat este controlat cu