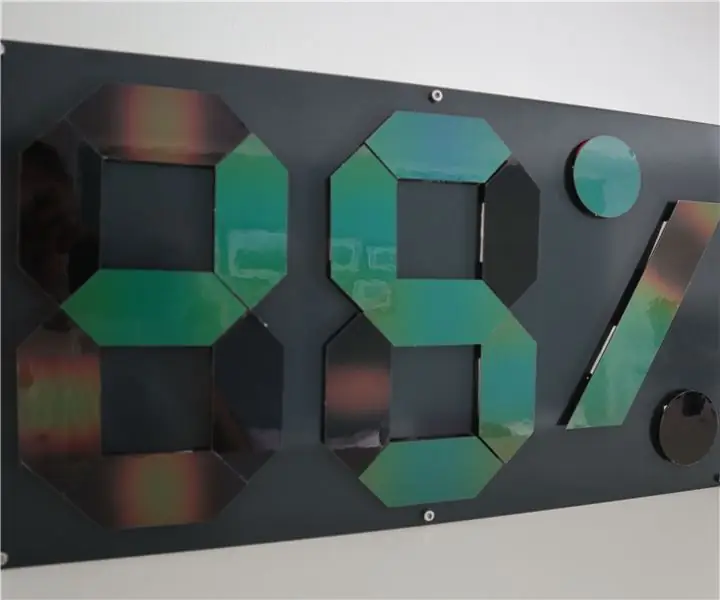
Cuprins:
- Provizii
- Pasul 1: Realizarea plăcilor de cupru
- Pasul 2: Atașarea foii de cristal lichid
- Pasul 3: Atașarea elementului TEC
- Pasul 4: Pregătirea plăcii de aluminiu
- Pasul 5: Atașarea segmentelor
- Pasul 6: Atașarea radiatoarelor și a suporturilor
- Pasul 7: Încărcarea codului
- Pasul 8: Cablarea nebuniei
- Pasul 9: Pregătirea plăcii acrilice
- Pasul 10: Proiect finalizat
2025 Autor: John Day | [email protected]. Modificat ultima dată: 2025-01-23 15:04
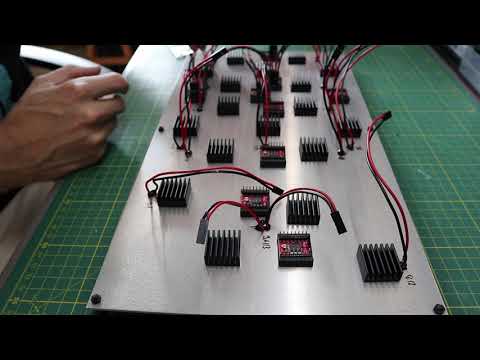
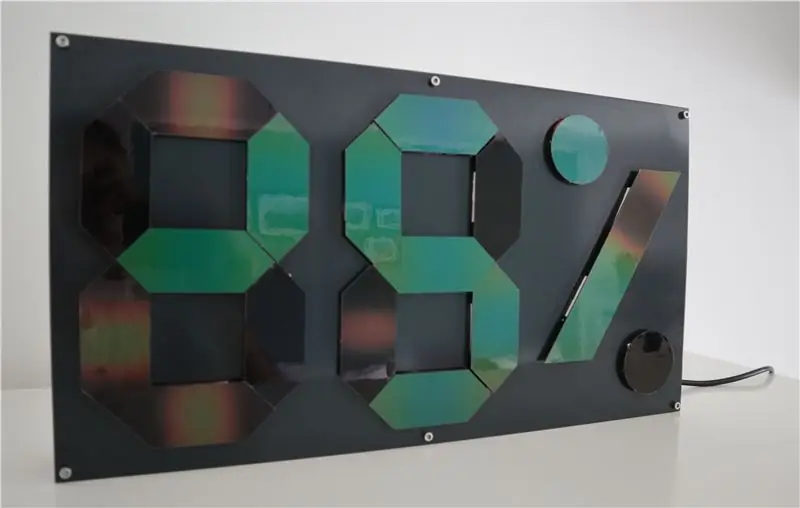

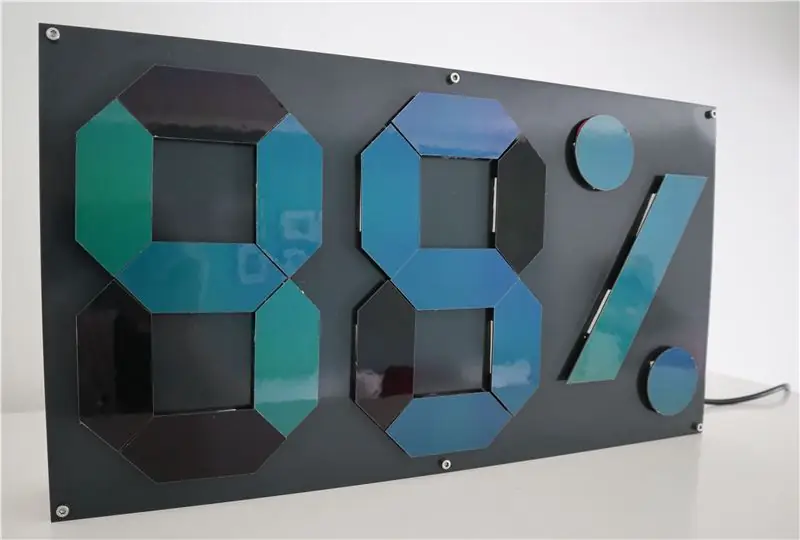
Lucrez la acest proiect de ceva timp. Ideea originală mi-a venit după ce am construit un demonstrator TEC controller la locul de muncă pentru un târg. Pentru a arăta capacitățile de încălzire și răcire TEC, am folosit vopsea termocromă care se schimbă de la negru la transparent.
În acest proiect am dus ideea mai departe și am construit un afișaj cu două cifre din 7 segmente, folosind plăci de cupru acoperite cu foi termocromice pe bază de cristale lichide. În spatele fiecărei plăci de cupru se află un element TEC care controlează temperatura și astfel schimbă culoarea foii de cristal lichid. Numerele vor arăta temperatura și umiditatea de la un senzor DHT22.
S-ar putea să apreciați ironia de a avea un dispozitiv care afișează temperatura ambiantă schimbându-și propria temperatură;-)
Provizii
- 3 buc, tablă de cristal lichid 150x150 mm (29-33 ° C) (vezi aici).
- 17 buc, plăci de cupru, grosime 1mm (dimensiunile vezi mai jos)
- Placă de aluminiu 401 x 220 x 2 mm (gri / negru anodizat)
- Placă acrilică 401 x 220 x 2 mm (alb)
- 18 buc, element TES1-12704 peltier
- 9 buc, driver dual motor TB6612FNG
- 6 buc, Arduino Nano
- 2 buc, ventilator de răcire 40x40x10 mm
- 18 buc, radiator 25x25x10 mm
- 12 V, 6 A sursă de alimentare
- Senzor de temperatură și umiditate DHT22 (AM2302)
- 6 bucăți, distanțe PCB de 40 mm lungime
În plus, am folosit acest epoxidic conductiv termic, care era destul de ieftin și are o durată lungă de viață. Un instrument de găurit și dremel a fost folosit pentru a face găurile necesare în plăcile de aluminiu și acrilice. Suportul pentru arduino și PCB-urile driverului de motor au fost imprimate 3D și atașate cu adeziv fierbinte. De asemenea, am folosit o mulțime de fire dupont pentru a face toate conexiunile. În plus, acest PCB cu terminale cu șurub a fost foarte util pentru a distribui sursa de alimentare de 12 V.
Atenție: Se pare că multe dintre plăcile TB6612FNG au instalate condensatoare greșite. Deși toți vânzătorii specifică placa pentru tensiuni ale motorului de până la 15 V, condensatoarele sunt adesea evaluate doar la 10 V. După ce am suflat condensatoarele de pe primele două plăci, le-am desoldat pe toate și le-am înlocuit cu altele adecvate.
Pasul 1: Realizarea plăcilor de cupru
Pentru plăcile de cupru am folosit un serviciu de tăiere cu laser online (vezi aici) de unde aș putea încărca fișierele dxf atașate. Cu toate acestea, deoarece formele nu sunt foarte complicate, tăierea cu laser nu este o necesitate și există, probabil, tehnici de fabricație mai ieftine (de exemplu, perforare, tăiere). În total, 14 dintre segmente, două cercuri și o liniuță sunt necesare pentru afișare. Grosimea plăcilor de cupru a fost de 1 mm, dar probabil ar putea fi redusă la 0,7 sau 0,5 mm, ceea ce ar necesita o putere mai mică de încălzire / răcire. Am folosit cupru, deoarece capacitatea termică și conductivitatea termică sunt superioare aluminiului, dar și acesta din urmă ar trebui să funcționeze rezonabil.
Pasul 2: Atașarea foii de cristal lichid
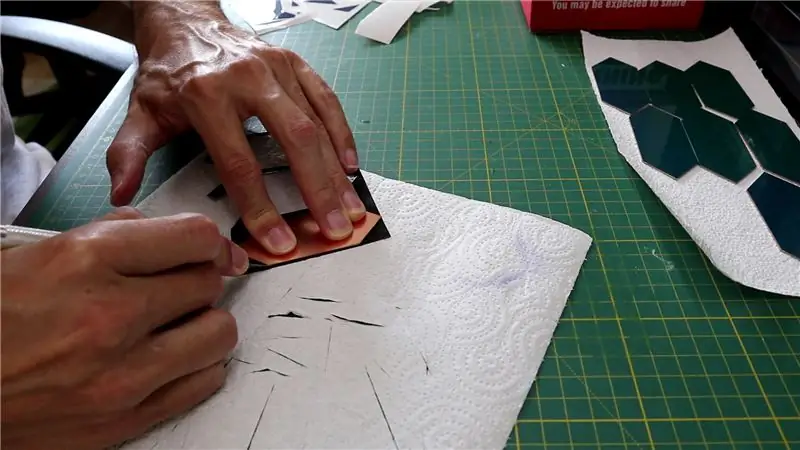
Componenta cheie a acestui proiect este folia de cristal lichid termocrom pe care am obținut-o de la SFXC. Folia este disponibilă în diferite intervale de temperatură și schimbă culoarea de la negru la temperaturi scăzute față de roșu, portocaliu și verde la albastru la temperaturi ridicate. Am încercat două lățimi de bandă diferite de 25-30 ° C și 29-33 ° C și am ajuns să le aleg pe acesta din urmă. Deoarece încălzirea cu un element mai plăcut este mai ușoară decât răcirea, intervalul de temperatură ar trebui să fie ușor peste temperatura camerei.
Folia cu cristale lichide are un suport autoadeziv care se lipeste foarte bine de placile de cupru. Folia în exces a fost tăiată în jurul plăcii folosind un cuțit exacto.
Pasul 3: Atașarea elementului TEC
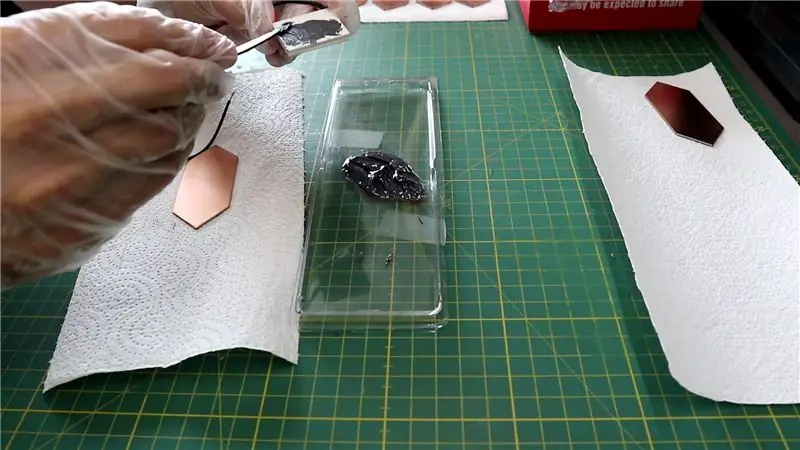
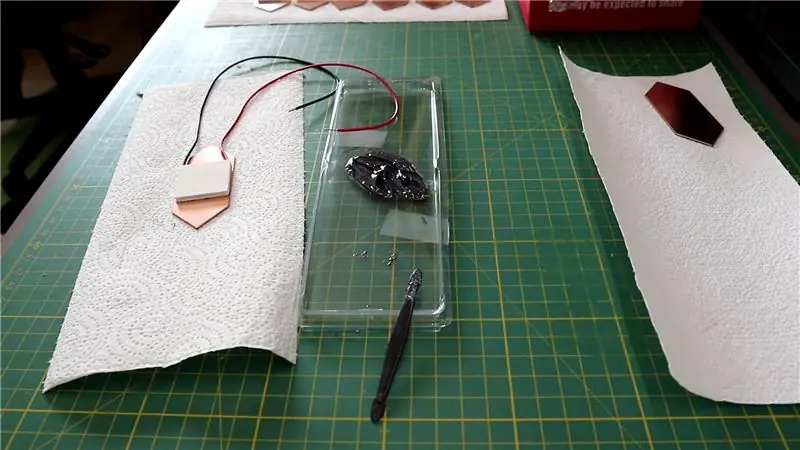
Peltierii au fost atașați la centrul fiecărei plăci de cupru folosind epoxidic conductiv termic. Plăcile sunt puțin mai mari decât peltiers, astfel încât să rămână complet ascunse în spate. Pentru placa mai lungă care constituie linia simbolului procentului, am folosit doi pieleți.
Pasul 4: Pregătirea plăcii de aluminiu
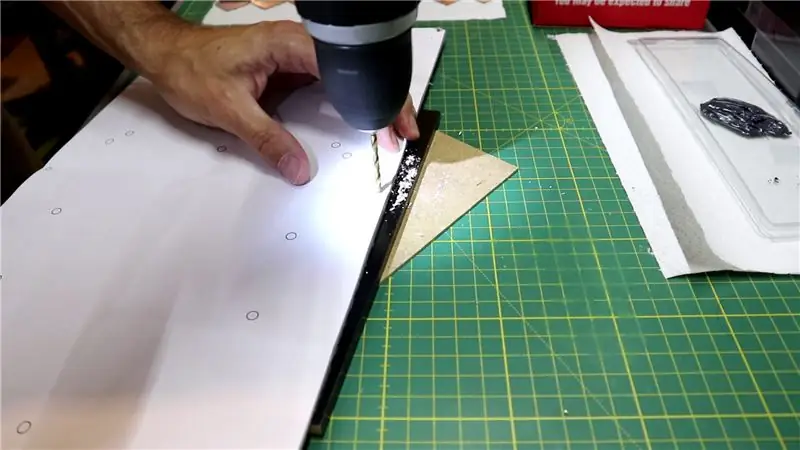
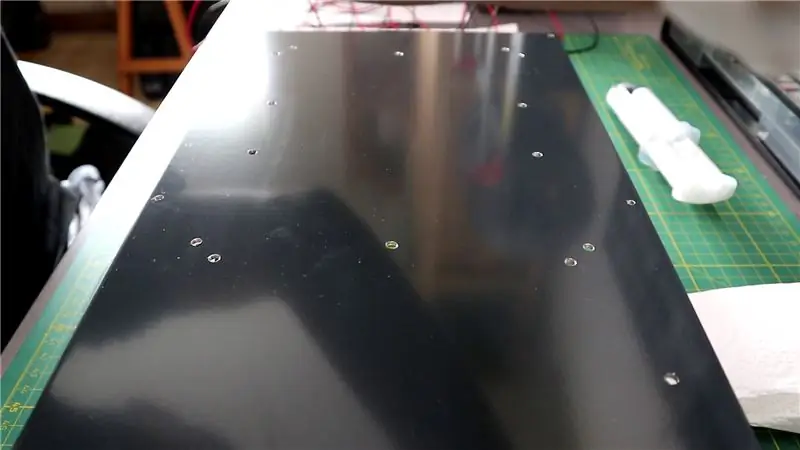
Pentru a economisi niște bani, am făcut eu toate găurile în placa de aluminiu. Tocmai am tipărit pdf-ul atașat pe hârtie A3 și l-am folosit ca șablon de foraj. Există o gaură pentru fiecare segment în care trec cablurile TEC și 6 găuri pe margini pentru fixarea ulterioară a plăcii acrilice.
Pasul 5: Atașarea segmentelor
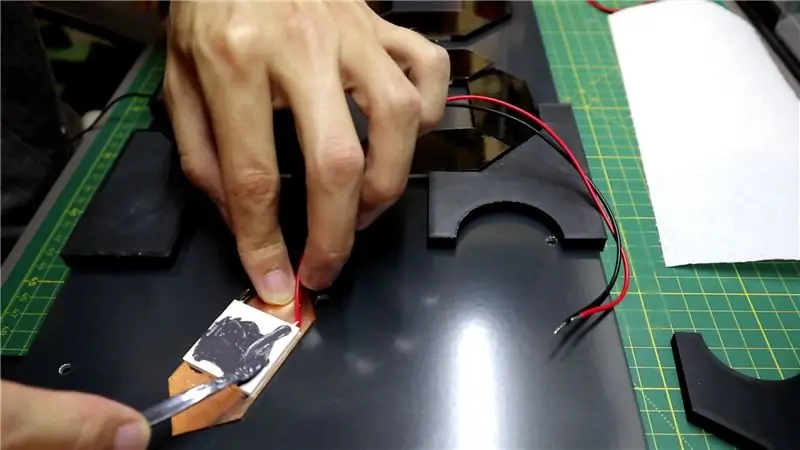
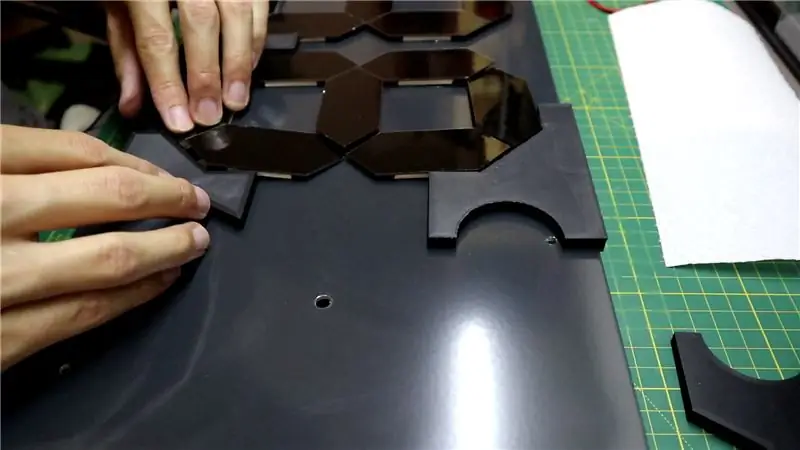
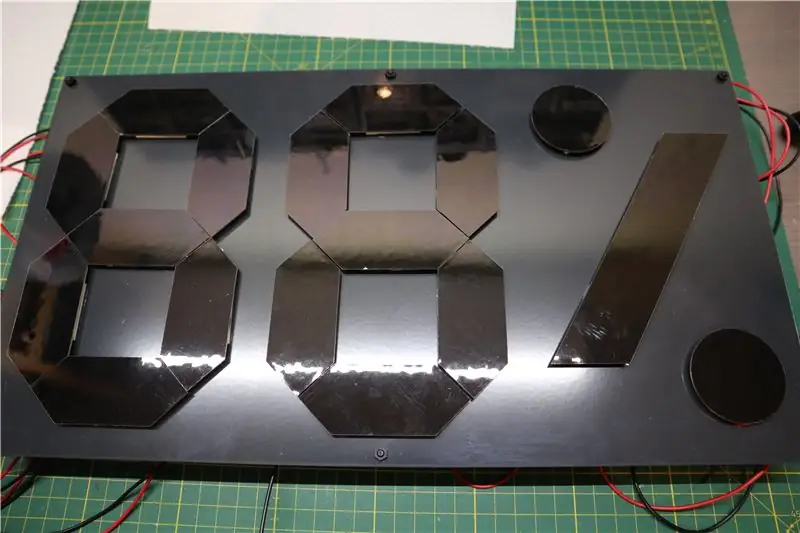
Una dintre cele mai dificile părți din acest proiect a fost atașarea corectă a segmentelor la placa de fundal. Am imprimat 3D mai multe jigs care m-ar ajuta cu alinierea segmentelor, dar acest lucru a funcționat doar parțial, deoarece segmentele alunecau constant. În plus, cablurile împing peltierul astfel încât să se desprindă de pe placă. Am reușit cumva să lipesc toate segmentele la locul potrivit, dar unul dintre peltiers din segmentul bordului are o cuplare termică foarte proastă. Ar putea fi mai bine să folosiți plăcuțe termice autoadezive în loc de epoxidice, deși bănuiesc că s-ar putea slăbi în timp.
Pasul 6: Atașarea radiatoarelor și a suporturilor
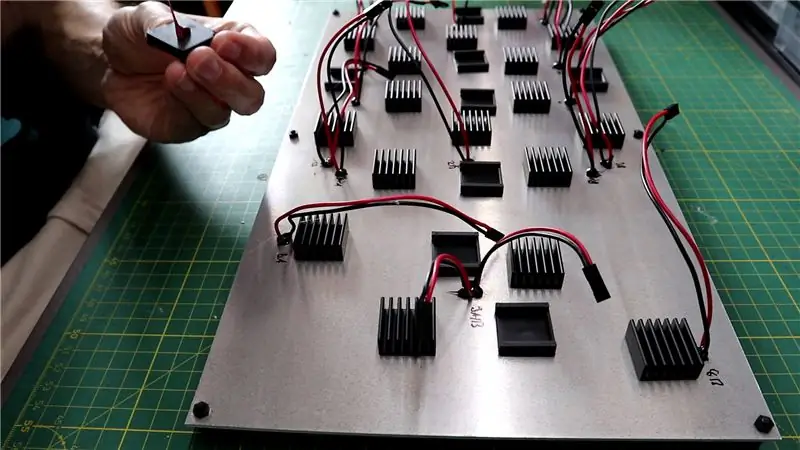
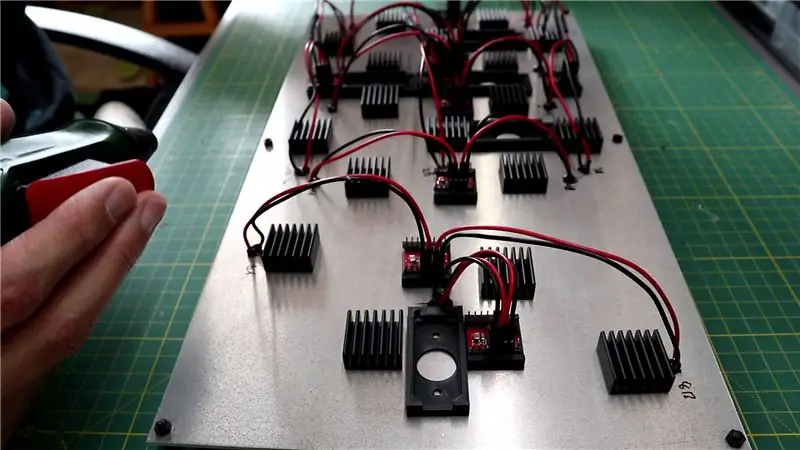
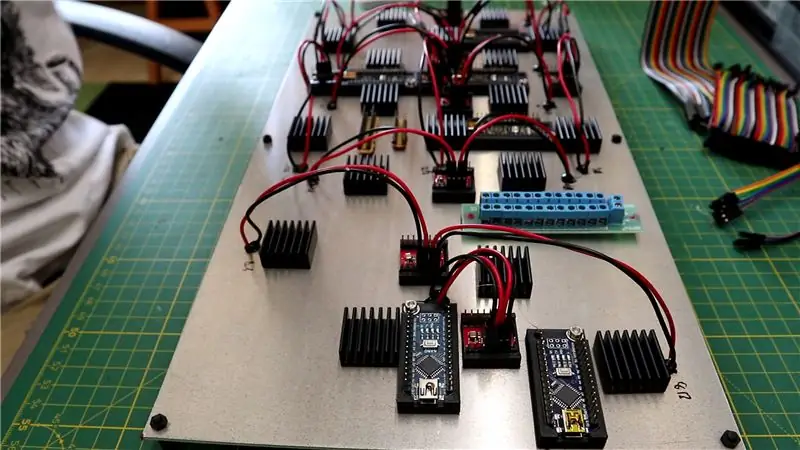
Ideea mea inițială a fost să folosesc doar placa de aluminiu ca radiator pentru peltiers chiar și fără ventilator. Am crezut că temperatura totală a plăcii va crește puțin, deoarece unele segmente sunt răcite, în timp ce altele sunt încălzite. Cu toate acestea, sa dovedit că, fără radiatoare suplimentare și fără ventilator de răcire, temperatura va continua să crească până la un punct în care plăcile de cupru nu mai pot fi răcite. Acest lucru este deosebit de problematic, deoarece nu folosesc termistori pentru a controla puterea de încălzire / răcire, ci folosesc întotdeauna o valoare fixă. Prin urmare, am cumpărat mici radiatoare cu un tampon autoadeziv care au fost atașate la partea din spate a plăcii de aluminiu din spatele fiecărui peltier.
După aceea, suporturile tipărite 3D pentru driverele de motor și arduino au fost, de asemenea, atașate la partea din spate a plăcii folosind hotglue.
Pasul 7: Încărcarea codului
Fiecare arduino poate controla până la doi șoferi de motor, deoarece au nevoie de doi PWM și 5 pini IO digitale. Există, de asemenea, drivere de motor care pot fi controlate prin I2C (vezi aici), dar nu sunt compatibile cu logica de 5 V a arduino-urilor. În circuitul meu există un arduino "master" care comunică cu 5 arduinos "slave" prin I2C care la rândul lor controlează driverele motorului. Codul pentru arduino poate fi găsit aici pe contul meu GitHub. În codul pentru arduino-urile „slave”, adresa I2C trebuie schimbată pentru fiecare arduino din antet. Există, de asemenea, unele variabile care permit schimbarea puterii de încălzire / răcire și a constantelor de timp corespunzătoare.
Pasul 8: Cablarea nebuniei
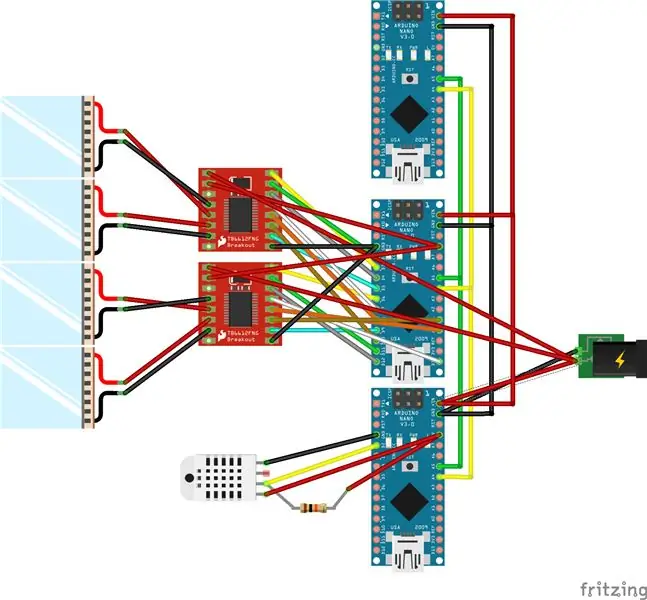
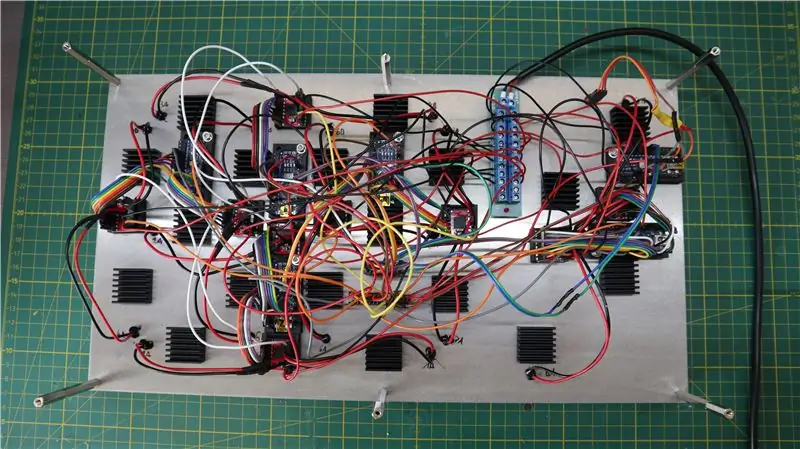
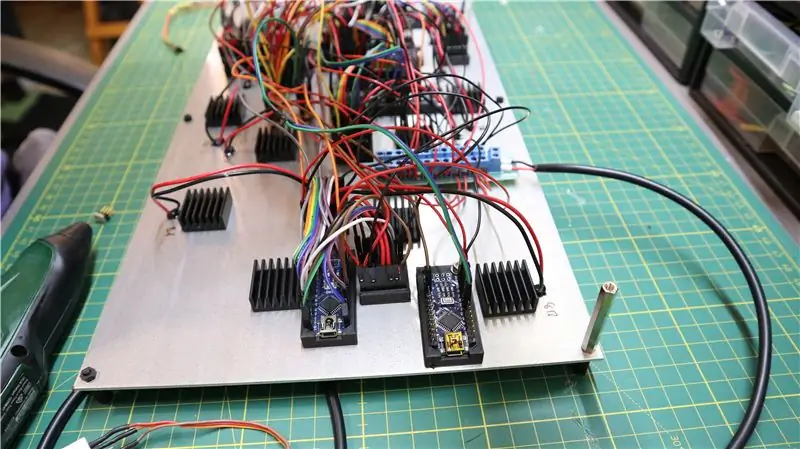
Cablarea acestui proiect a fost un coșmar total. Am atașat o diagramă fritzing care arată conexiunile pentru arduino master și un singur arduino slave, ca exemplu. În plus, există un pdf care documentează ce TEC este conectat la ce driver de motor și arduino. După cum puteți vedea pe imagini datorită cantității mari de conexiuni, cablarea devine foarte dezordonată. Am folosit conectori dupont oriunde a fost posibil. Sursa de alimentare de 12 V a fost distribuită folosind un PCB cu borne cu șurub. La intrarea de alimentare am atașat un cablu de curent continuu cu cabluri zburătoare. Pentru a distribui conexiunile de 5 V, GND și I2C, am echipat niște prototipuri PCB cu anteturi pin masculine.
Pasul 9: Pregătirea plăcii acrilice
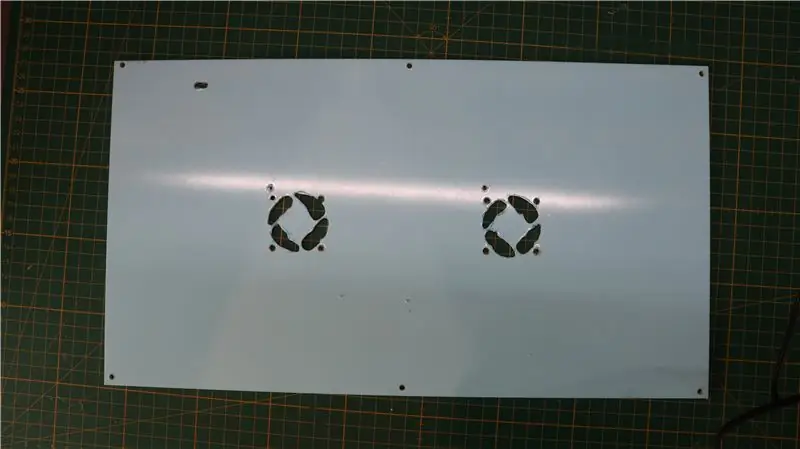
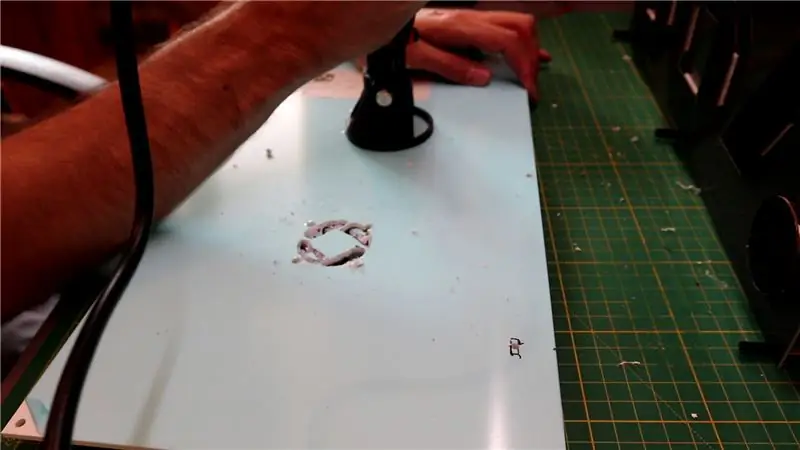
Apoi, am făcut câteva găuri în placa acrilică, astfel încât să poată fi atașată la placa de aluminiu prin intermediul standoff-urilor PCB. În plus, am făcut câteva decupaje pentru ventilatoare și o fantă pentru cablul senzorului DHT22 folosind instrumentul meu dremel. După aceea, ventilatoarele au fost atașate la partea din spate a plăcii acrilice și cablurile au fost introduse prin câteva găuri pe care le-am forat. Data viitoare voi face probabil placa prin tăiere cu laser.
Pasul 10: Proiect finalizat
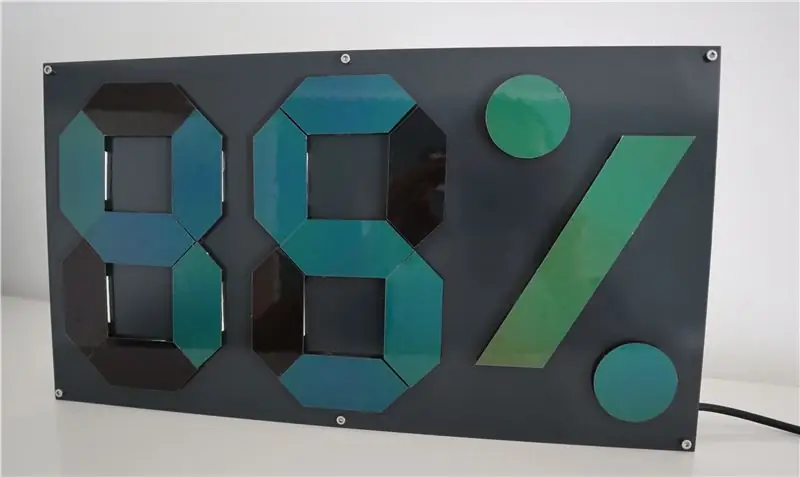
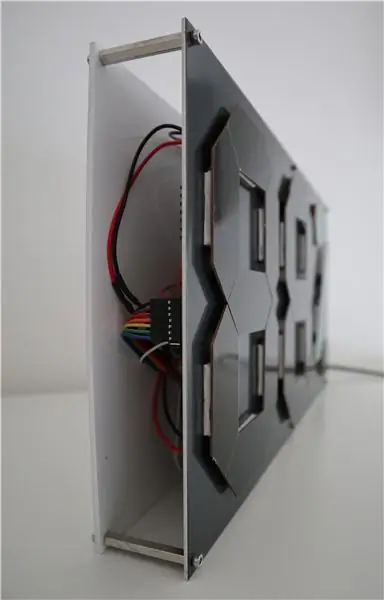
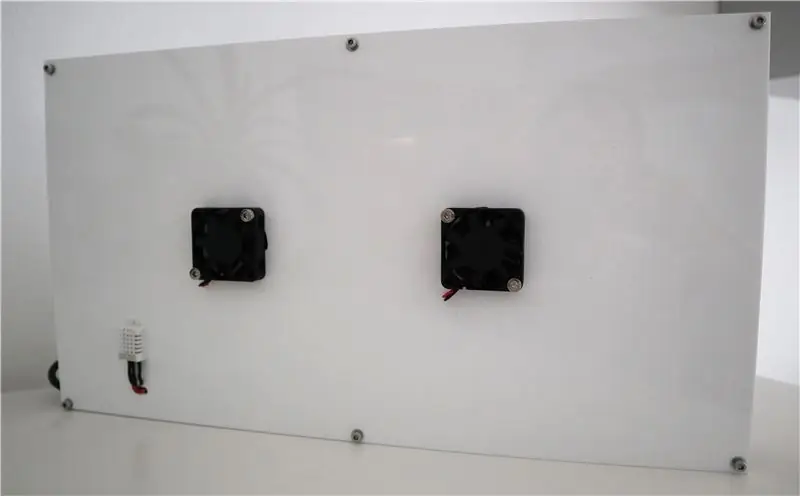
În cele din urmă, placa acrilică și placa de aluminiu au fost atașate una cu cealaltă folosind distanțe PCB de 40 mm lungime. După aceea, proiectul este terminat.
Când sunt conectate la sursa de alimentare, segmentele vor arăta temperatura și umiditatea alternativ. Pentru temperatură, numai punctul superior își va schimba culoarea, în timp ce liniuța și punctul inferior sunt evidențiate când se arată umiditatea.
În cod, fiecare segment activ se încălzește timp de 25 de secunde, în timp ce se răcesc simultan segmentele inactive. După aceea, peltiers sunt opriți timp de 35 de secunde, astfel încât temperatura să se stabilizeze din nou. Cu toate acestea, temperatura plăcilor de cupru va crește în timp și va dura ceva timp până când segmentele vor schimba complet culoarea. Extragerea de curent pentru o singură cifră (7 segmente) a fost măsurată la aproximativ 2 A, astfel încât consumul total de curent pentru toate segmentele este probabil aproape de maximul de 6 A pe care îl poate furniza sursa de alimentare.
S-ar putea reduce cu siguranță consumul de energie adăugând termistori ca feedback pentru a regla puterea de încălzire / răcire. Un pas mai departe ar fi să folosiți un controler TEC dedicat cu buclă PID. Acest lucru ar trebui, probabil, să permită o funcționare constantă fără un consum mare de energie. În prezent mă gândesc să construiesc un astfel de sistem folosind driverele Thorlabs MTD415T TEC.
Un alt dezavantaj al configurației actuale este că se poate auzi ieșirea PWM de 1 kHz a driverelor motorului. Ar fi, de asemenea, frumos dacă s-ar putea scăpa de fani, deoarece sunt și ei destul de puternici.
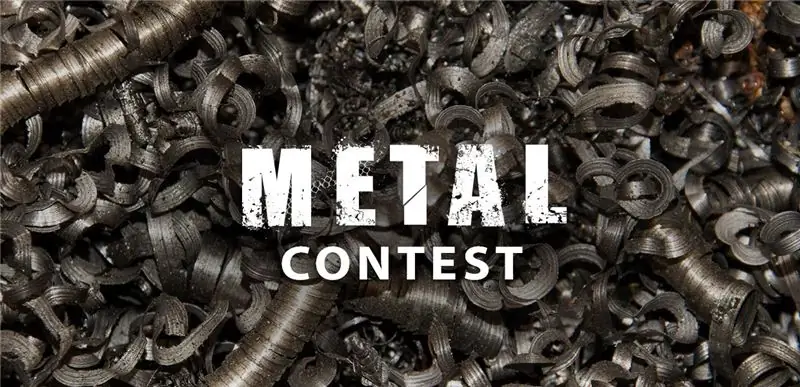
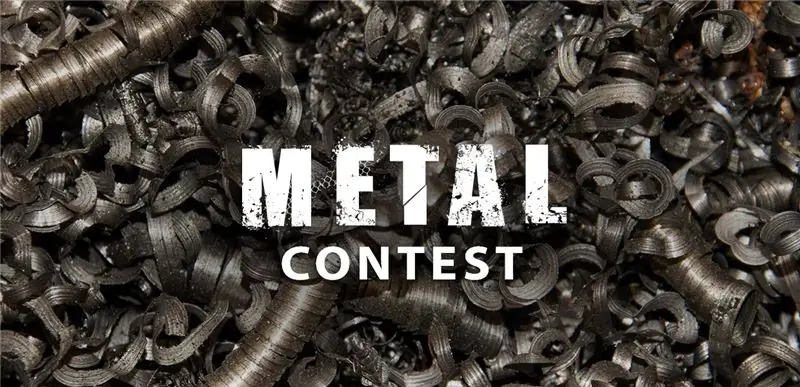
Premiul I la Concursul de Metal
Recomandat:
Afișaj de temperatură și umiditate termocromă - Versiune PCB: 6 pași (cu imagini)
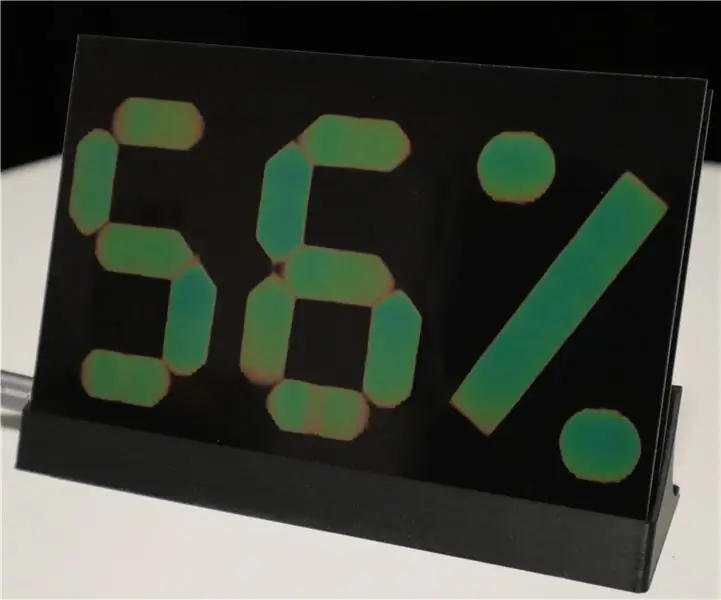
Afișaj de temperatură și umiditate termocromă - versiunea PCB: Cu puțin timp în urmă a făcut un proiect numit Temperatură termocromă & Afișaj de umiditate în care am construit un afișaj cu 7 segmente din plăci de cupru care au fost încălzite / răcite de elemente mai groase. Plăcile de cupru au fost acoperite cu o folie termocromică care
Automatizarea unei sere cu LoRa! (Partea 1) -- Senzori (temperatură, umiditate, umiditate a solului): 5 pași
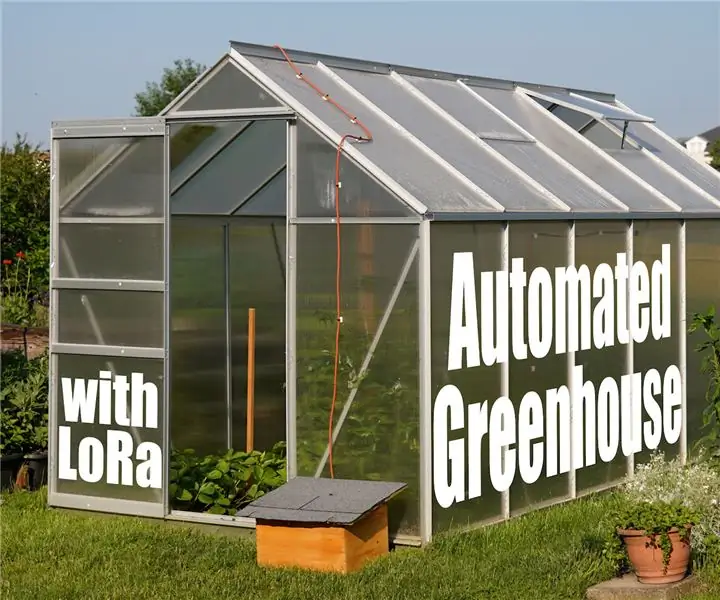
Automatizarea unei sere cu LoRa! (Partea 1) || Senzori (temperatură, umiditate, umiditate a solului): În acest proiect vă voi arăta cum am automatizat o seră. Asta înseamnă că vă voi arăta cum am construit sera și cum am conectat electronica de putere și automatizare. De asemenea, vă voi arăta cum să programați o placă Arduino care utilizează L
Senzor de temperatură și umiditate cu afișaj Arduino și Lcd: 4 pași
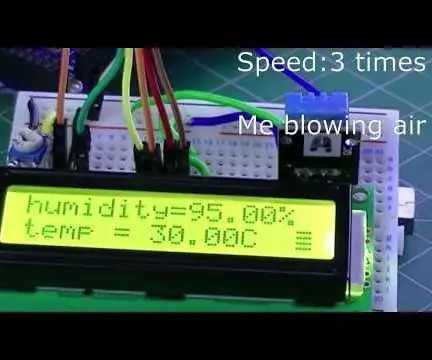
Senzor de temperatură și umiditate cu afișaj Arduino și Lcd: Bună, băieți, Bine ați revenit la Artuino. După cum ați văzut, am început Un InstructableToday vom face o temperatură & Umidometru cu modulul DHT11. Să începem PS. Luați în considerare Abonarea și aprecierea videoclipului
Afișaj umiditate temperatură Arduino 24 de ore: 3 pași (cu imagini)
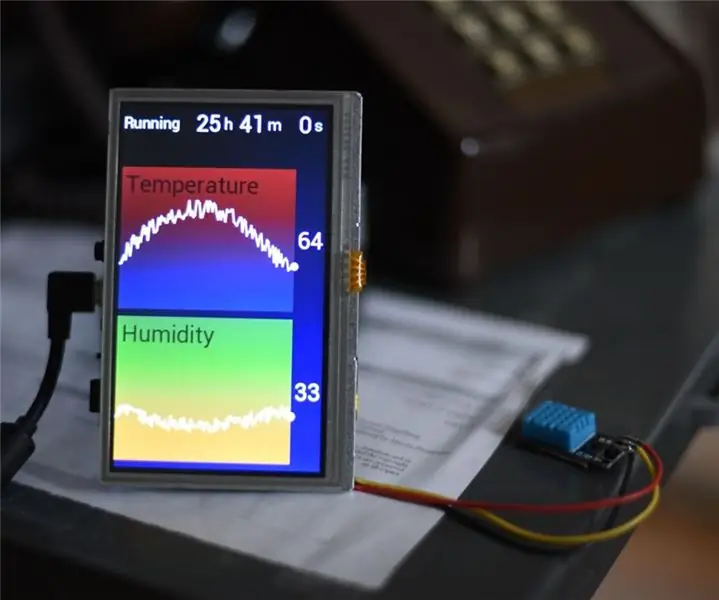
Afișaj de umiditate a temperaturii Arduino 24 de ore: DHT11 este un senzor excelent pentru a începe. Este ieftin și ușor de conectat la un Arduino. Raportează temperatura și umiditatea cu o precizie de aproximativ 2%, iar acest instructabil folosește un Gameduino 3 ca afișaj grafic, care arată 24 de ore de istorie.W
Înregistrare internet de temperatură și umiditate cu afișaj utilizând ESP8266: 3 pași
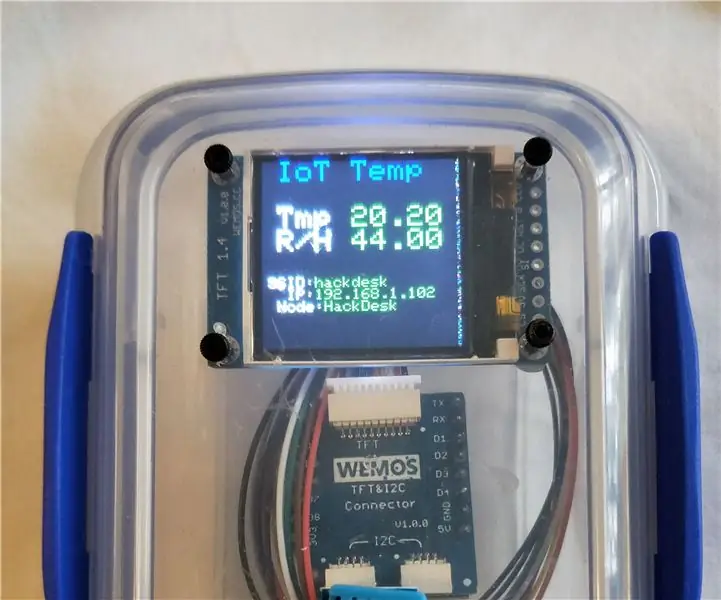
Înregistrare internet pentru temperatură și umiditate cu afișaj utilizând ESP8266: Am vrut să împărtășesc un mic proiect care cred că vă va plăcea. Este un jurnal de internet de temperatură și umiditate mic, durabil, cu afișaj. Aceasta se conectează la emoncms.org și, opțional, fie local, la un Raspberry PI, fie la propriul dvs. emoncm